**************************************
INDEX 1
2 3
4 5 6
7 8
9
4章 高速度電動機
4.1 電動機の軽量小型化 top
電動機のサイズと重量を減少する主たる要素は電機子に高速度を許し得る歯車装置にある。
従来の直接駆動方式においては、前述の通り釣掛式の許し得る最大歯車比という絶対的制限の故に、歯車比の最大はせいぜい5:1であった。
電動機をバネ吊りとして車軸から分離する分離駆動方式によると、歯車装置に無理がかからなくなり、歯車比は電機子の回転し得る最高経済速度まで選択出来ることとなって歯車装置の形式如何によっては 12 : 1 程度まで許し得ることになった。
一般に電動機のサイズと重量はほぼ回転力に比例する。
また馬力は(2.8)式より回転数と回転力の積に比例する。すなわち(2.2)式より
出力=E=(p/a)Zφ(n/60)I×10の−8乗(W)…………4.1式
pφは全磁束数で電機子直径Dmと電機子鉄心長Lmに比例する。
(I/a)Zは電機子アンペア導体数で電機子直径Icmに比例する。
従って
出力/回転数=常数×回転カ=K1(Dの2乗Lc)のk2乗…………4.2式
Lc:電機子鉄心長(cm)、K1、K2:常数
Dの2乗Lcは電機子サイズを表わす故、電機子サイズは回転力にほぼ比例する。
従ってある馬力の電動機がより大なる回転数と、より小なる回転力に設計されるとすればその電機子は小さな回転力に比例して小型となる。
分離駆動方式の初期試験時代における高速度電動機は、釣掛式における軽量化の経験を基礎として設計されたものであったので、何れも無雑な構造であった。
その後の多数の設計経験、製作経験、使用経験と研究とにより最近の高速度電動機はますます洗練された構造となって小型化しつつある。
さらに最近の電動機において電機子を小型軽量になしうる他の理由は電機子巻線のより薄い、より強い、マイカ・ガラスおよひラッパーなど絶縁物の進歩によるスペースの節減である。
これらのスペースの節減が電機子サイズを小型化出来る結果、さらに電機子回転数を高い値まで上げることができ、従ってさらにまた電機子を小型化することが可能となる。
電機子の小型化は同時に界磁のサイズも小さくできるので電動機全体として小型軽量となる。
一般電動機全体の重量は(定格トルク)の2/3乗、または(HP/rpm)の2/3乗にほぼ比例するものである。
4.1図は最近の釣掛式電動機と最新の高速度電動機の重量の比較を示す。 |
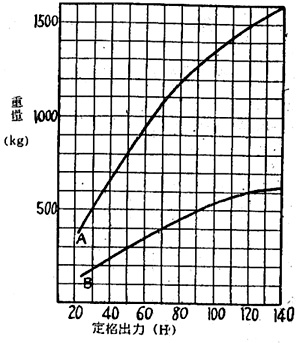
4.1図 電動機重量の比較
|
4.2図は最近の電動機について回転数と馬力と重量との関係を示すノモグラフである。
電動機軽量化による決定的な利益は材料の節約にある。
例えばアメリカにおける3,000両のPCC電車の鋼材の節約料は、これを同馬力の釣掛式電動機と比較した場合実に820tに達するといわれる。
さらに電動機を小型軽量化することから生ずる他の間接的な大きな利益は必然的に台車構造を小型軽量化できることである。
これらの所要資材の節減による直接および間接的利益と軸重軽減によるレールおよび道床に与える利益は、けだし甚大なものであることは銘記する必要があろう。
4.2 スペシフィック・スピード・レショ・パワー
top
一般に電気車用電動機は低速度の定格が必要であるとともに、さらに定格速度の2〜5倍の範囲の最高速度で運転され得る能力をも必要とする。
最高速度/定格速度=速度比(スピード・レショ)とすると、ある仮定を設ければこの速度比が、たとえば、5の電動機は最高速度においてのみ同一定格出力を出し得る仮想的電動機の5倍の引張能力がある筈である。
最初は軽量であることを目標とし、この線に沿ってなしとげられた高速度電動機の進歩を評価する一つの尺度として、最近スピード・レショ・パワー(略してSRPという)がアメリカにおいて用いられはじめた。
SRP=速度比×定格容量
=(最高許容速度/定格回転数)×定格容量
このSRPは電動機の実際使用上の能力を表わしている。
車両の起動加速度は一般にSRPに比例することは次のように考えれば諒解できる。
すなわち上式をさらに展開すると |
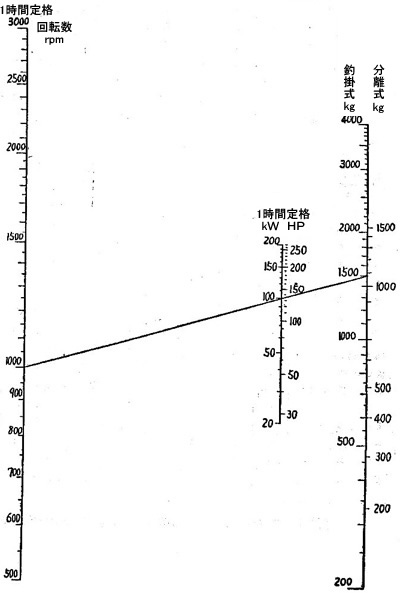
4.2図 電車電動機の重量(1時間定格)
|
SRP=最高許容回転数×(定格容量/定格回転数)∝最高許容回転数×定格トルク
となる。
車両が最高安全速度のときに電動機が最高許容回転数になるように歯車比を定めると、上式はさらに
SRP=((歯車比/車輪径)×車両最高安全速度)×定格トルク
=((歯車比/車輪径)×定格トルク)×車両最高安全速∝定格引張力×車両最高安全速度
となるから車両の最高安全速度を定めると、SRPは定格引張力に比例し、また起動引張力にほぼ比例することがわかる。
従って車両のトン当り馬力を定めると、起動加速度はSRPにほぽ比例することになる。
換言すれば実際運営上SRPが大きいほど、それだけ馬力が大きくなったことと同じである。
従って電動機の能力は馬力そのものよりも、SRPによって比較すべきである。
次にSRPに電動機重量の因子を加味するため単位重量当りのSRPで表わすと、電動機設計の優劣の比較と電動機進歩の比較の尺度として適切であるので、筆者はこれを |
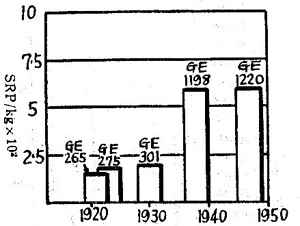
4.3図 600V多編成用電動機の進歩 |
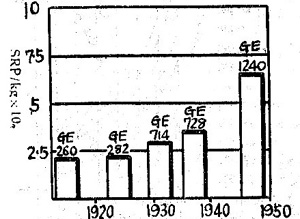
4.4図 600V路面電車の進歩
|
スペシフィック・スピード・レショ・パワー(Specific Speed
Ratio Power)と仮りに呼称しておく。
SSRPは次の式で表わされる。
SSRP=(最高許容速度/定格回転数)×定格容量×(1/重量)
SRPおよびSSRPを代表的な電動機について比較すると4.1表に示す値となり、SSRPによって、GE製電動機の進歩の推移(13)を示したものが4.3図および4.4図である。
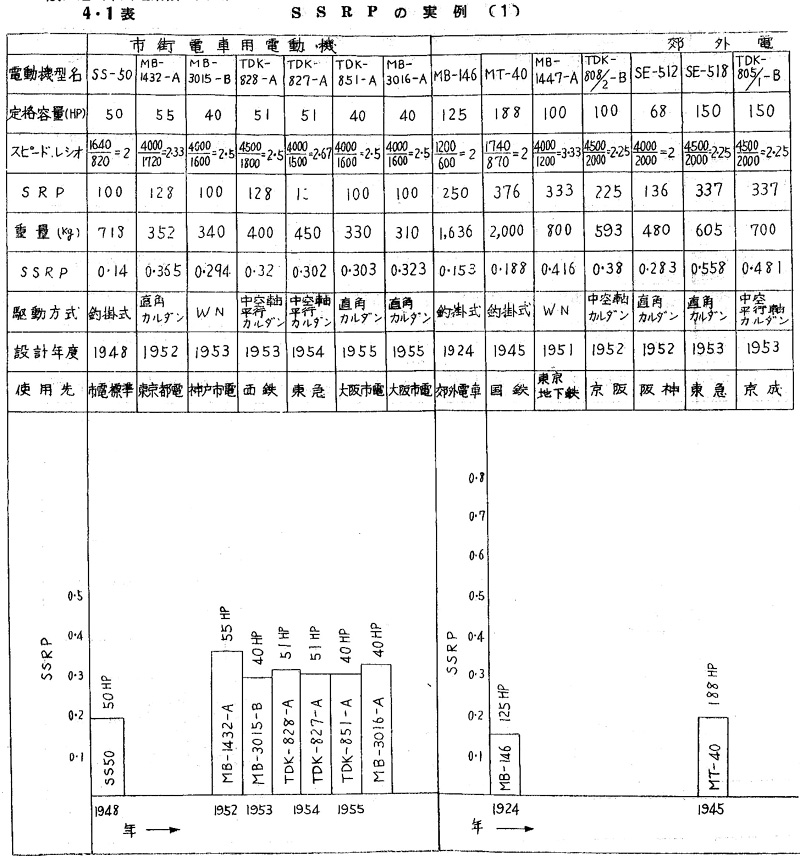
4.3 発電ブレーキの常用
top
4.3・1 発電ブレーキの必要性
運転の安全確実と高加速度、高減速度が電気車に要求されるようになって電動機による発電ブレーキが常用されるに至った。
制輪子と車輪との間の摩擦係数に頼る従来の空気ブレーキ方式では
(1) 4.5図の如く摩擦係数が速度により一定でなく、強力なプレーキカを必要とする高速度において摩擦係数が小さいという全く逆の傾向の特性を示すことは空気ブレーキ方式の大きな欠点であるが、発電プレーキは速度の如何にかかわらず、ブレーキカは一定である。 |
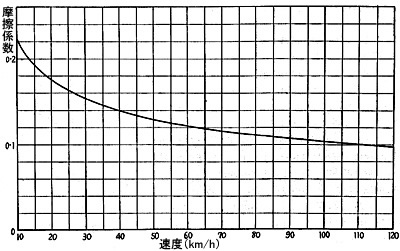 |
(2) 制輪子から飛散する鉄粉が電動機制御器具、その他に飛込んで絶縁を低下させ、故障を誘発する原因となり、電動機ならびに制御器具の設計、工作および材料の進歩による高い信頼度にもかかわらず、これらの鉄粉が故障の原因となり、保守費の増大を来たしている。また制輪子の摩耗と制輪子の取換えはまた、保守費のかさむ原因である。
(3) 一般にブレーキ操作から、ブレーキ作用までの空走時間が発電ブレーキは短かくでき、特に高速においても安定であるので、プレーキの信頼度が高い。
これらの理由で電気ブレーキの常用は最近の高性能電気車の欠くべからざる必要条件となるに至った。
4.3.2 発電ブレーキと電動機 top
発電ブレーキの常用は電動機にとっては2乗平均RMS(Root Mean Square)電流の増加となって負担を重くすると共に、電気車の高速度からの発電ブレーキは、その誘起電圧が過大となって整流を悪くし閃絡をおこす危険さえある。
電動機をバネ吊りすることによってレールからの衝撃から電動機は開放され、衝撃による閃絡の危険がなくなり、発電プレーキに好都合となったが、さらに高速度において強力なる電気ブレーキカを発生するためには、過大な誘起電圧に耐えるよう特殊な設計上の考慮が電動機に必要である。
直巻電動機の力行の時の出力負担は前述の如く、起動においては大きな起動回転力を必要とするが速度が小さく、高速になると、その反対に回転力が小さい。
すなわち、自ら出力の調節作用を営んで出力の過大負担を避けているが、ブレーキの時の高速度からの発電プレーキは、高速と大ブレーキ電流との相乗積となって出力の過重と誘起電圧の過大を招き整流を悪くするなど、非常に苛酷な負担となる。
従って電動機の設計はこのような苛酷な負担に耐え得られるよう、充分考慮の必要がある。
ニューヨーク地下鉄の1947年製作の新造車は600Vの第3軌条電圧に対し300V端子電圧で100HPの電動機を4台取付けているが、この電車の発電ブレーキカは 67km/h以上の高速において最大となるよう設計されている。
この最大ブレーキカの時の発電機として作用する電動機馬力は 340HPであって、1時間定格馬力の実に 3.4倍となっている。
4.3.3 過電圧耐量 top
従来の電動機の過電圧耐量は定格電圧の110〜120%が許容限度とされていたが、最高速度において強力な電気ブレーキカを発生するためには過電圧耐量は
スピード・レシオ=(最大回転数/定格回転数)×100%
までの過電圧に安全であることが必要となった。
このような耐過電圧電動機の設計の要諦は低整流子片間電圧と良好な整流の保証にある。
一般に平均整流子片間電圧は次の式で表わされる。
ek=EP/Nk…………4.3式
ek:平均整流子片間電圧
E:電動機端子電圧
P:極数
Nk:整流子片数
従って平均整流子片間電圧を低く保つためにはEを小さくNkをできる限り多くどれるよう努力する必要がある。
@ Eを小さくするためには、1,500Vの架線電圧に対しては、375Vの端子電圧に設計すること。
A Nkを大きくするたのには、従来の波巻よりも重ね巻きの巻線方式が好適である。
B Nkはできる限り大きく設計したいが、高速度電動機では整流子も小型であるので、枚数にも限度があり、無闇に大きくはできない。
4.3.4 発電ブレーキと電動機出力
top
電気ブレーキを常用とする場合には力行のみ行う場合に較べて、RMS電流が増大し所要の電動機容量も大きくなる。
電気プレーキによる容量の増大は駅間距離・停車回数・停車時間・減速度・列車速度制限区間でのブレーキカとブレーキ回数・1ブレーキ時間などの運転状件によって異なり一様ではないが、一般には力行のみの場合より20〜30%の容量の増加で充分であるのが通例である。
右上の4.9図は発電ブレーキを常用する場合の運転前線と、RMS電流増大との関係を示す一例である。
4.3.5 発電ブレーキと電動機磁気音
高速において発電ブレーキを適用すると電動機から高周波の磁気音を発生することがある。
これは高速大電流のために、電動機の主極片と電機子鉄心の歯との間の磁束の脈動により発生する磁気音である。
これを防ぐには電機子鉄心のスロットをスキュ−するか、4.10図またはスロットは電動機軸に平行のままで主極の極片の形状および電機子表面との間の空隙の形状を工夫すれば避け得られる。
ただし、スロットをスキューすると電機子巻線をスロットに納める工作が厄介になるのと、補極の下の整流帯が広がって整流を悪くするという欠点があるので後者による方法の方が望ましい。 |
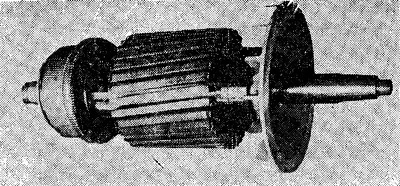
4.10図 スキュー(ねじる)した電機子鉄心
|
4.4 整流 top
直流電動機の良否は整流如何にあるといっても過言ではないので設計者は良好な整流を得るようあらゆる努力を払っている。
一般に電動機の電機子・巻線・主極・補極・空隙・整流子・ブラシなどの電気的設計も機械的設計もその目標は良好なる整流の保証に帰一するといっても過言ではない。
最近の高速度電動機のように、高速度における発電ブレーキの常用ということと、この事項に適するよう設計常数を選んで、しかもなお運転の広範囲の条件のもとで安定した整流を保証することは、整流の責務としては誠に峻厳極まるものである。
スピード・レショの増大は低速度から高速度までの主電動機の有効馬力限界の拡大であり、弱界磁から全界磁の全域にわたっての整流範囲の拡大に対しても良好な整流を保証していることを意味する。
このように高速度における最大発電ブレーキという条件で設計しておくと、力行の時にはむしろ整流条件としてはやさしいこととなり、パンタグラフの離縁による電流遮断から再印加などの電圧急昇あるいは、サージに対して安定した整流を示している。
一般に補極を設けてブラシに火花を発生させる原因となるリアクタンス電圧を打ち消すのであるが、リアクタンス電圧は時間的に変化するものである。
従って、これを補極の磁束で打消すとしても、整流周期中を通じて完全に打消すことは至難で、幾分は打ち消し切れない残余の電圧がある。
この残余の電圧をなるべく小さくするには、リアクタンス電圧そのものを小さくすればよい。
整流周期中にその巻線素子に生ずる平均リアクタンス電圧は
(Er)mean=(L+狽l)Ie/Tk(V)…………4.4式
Le :正負各1列のブラシに流れる電流(A)
Tk:整流周期(sec)
(L+狽l):1個の短絡素子の自己インダクタンスおよび相互インダクタンス(H)
(Er)mean:平均リアクタンス電圧(V)
(L+狽l)はその短絡素子に1アンペアの電流が流れた場合に溝内およびコイル・エンドなどに生ずる漏洩磁束を見出せば算出することができる。
リアクタンス電圧の実験式については Lamme 氏などによって提案されているが(L+狽l)は電機子コイルの1整流子片に接続される素子の巻回数の2乗に正比例し、ブラシ・カバリングに比例するほか電機子導体1巻きの平均長にも関係する。
従って良好な整流を得るためには次の条件が必要である。
(1) 整流周期Tkを長くすることが望ましい。すなわち、回転数が大きいと整流が困難になる。
(2) 電機子導体の1巻きの長さを短くするほど良い。
整流上の見地からは電機子の直径を大きくして鉄心の長さを短くした方が有利である。
高速度電動機は電機子の導体数は少くなく、導体も短いのでこれが速度上昇による整流阻害の要素を多少なりとも打消している。
(3) 電機子コイルの1個の素子の巻回数は1回巻が望ましい。
もちろん高速度電動機の場合には1回巻とし、できるだけ整流子片数を増加しで同時に整流をうける巻数を減少させる。
(4) 整流子片の増加によるプラシ・カバリングの増大に対しては、割り型ブラシを使用すると良い。
(5) ブラシの接触抵抗を大きくすると、直線整流となり、整流は良好となる。
補極によって、短絡コイルに整流に必要な電圧を誘起させて、整流を促進する電圧整流だけではリアクタンス電圧を完全に補償することは困難であるから、接触抵抗の大きいブラシを使用して、電圧整流と、抵抗整流とを併用する。
この意味においてブラシの選択はきわめて重要である。
(6) 整流帯は主極磁束の分布の影響を受けないように、充分主極から遠ざかるよう考慮する。
すなわち、整流帯と主極との間隔――これをシングル・クリアランスという――を広く設計する必要がある。
普通同一のスロット幅に数本のコイル辺がまとめて入っているが、この場合には、これら全部のコイル辺が同一の捕獲の影響を受けて整流を完了しなければならない。
このためには全整流周期幅に電機子の諭く距離だけ整流磁界が存在しなければならない。
この全部のコイルについて整流が始まってから終了するまでにスロットの動く距離に相当する整流帯の幅はプラシの厚さとスロット内で横にならぶ導体数に関係する。
これらの値をあまり大きくすると整流体の幅は著しく広くなり、ついには主磁束の影響下に入り、完全な補極磁束分布を乱して整流不良を起す。
(7) ポ−ル・アークは小さくすることが望ましい。これは漏洩磁束の影響をなくするためにも必要である。
(8) 捕獲と磁気ウクは高速時の電気プレーキの際の最大電流に対し補償不足とならないよう、また、力行時の全界磁制御から弱界磁制御への広い速度範囲において整流を良好にし、無火花整流帯の幅を最大にするためにも捕極と磁気枠は低い磁気飽和に設計しておく必要がある。
整流の良否はその原因が複雑であるから、りアクタンス電圧の大小のみによってこれを判定することは困難であるが、高速度電動機に対しては5〜6V以下が望ましい。
4.11図はリアクタンス電圧について従来の低速度電動機と最近の高速度電動機とを比較したものである。
アメリカのGE社はリアクタンス電圧に相当する整流阻害の因子を次の如く規定してリアクタンス電圧1次指数と称し、同じ整流特性に対して、この指数の高い程よい設計の電動機としてその比較の一つの尺度としている。
GEの提唱するリアクタンス電圧1次指数としては次の式によるものである。
Le・Ie・wの2乗・Z・Nk…………4.5式
w:整流子片に接続される電機子コイルの素子の巻回数
Nk:整流子片数
4.12図はこの指数について従来の釣掛式電動機と最近の台車装荷電動機との比較である。
図は1904年に製作されて、New York 地下鉄に納入されたGE−69形電動機と、1948年に製作されて同様にNew York地下鉄に納入されたGE−1240形とのリアクタンス電圧1次指数の進歩の模様を表わしていて、GE−1240形が最高速度における最高電気ブレーキ電流という電動機にとって苛酷な悪条件にあるにもかかわらず、高いリアクタンス電圧1次指数を有していることは大いに注目すべき最近の設計というべきである。 |
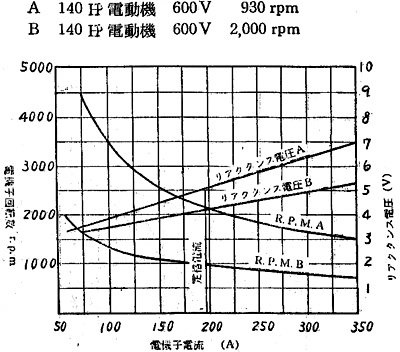
4.11図 リアクタンス電圧の比較
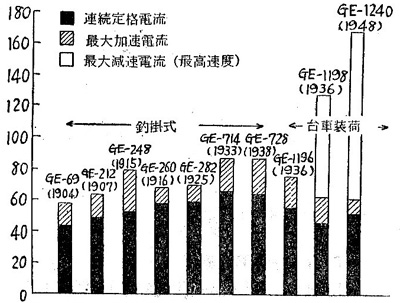
4.12図 リアクタンス電圧1次指数の比較
|
4.5 弱界磁制御と弱界磁定格 top
4.5.1 弱界磁率の増大
直巻電動機は速度が上昇すれば、急激に出力が低下する。
従って弱め界磁によって高速における出力の低下を緩和して速度の増大をはかるので弱界磁率を増すことは、馬力の増大と同等である。
さらにこれを詳説すれば、高速度においては電流が減少するから引張力も減る。
そこで弱界磁をすれば、電流を増して引張力を増す。この関係は2.2式より
n=(E−IR)/(PZφ/60a)×10の−9乗 E=kφn+IR………4.6式
となる。いま(4.6)式について考えてみると、E と n とが一定なれば φ も矢張り一定である。
弱界磁にすると、瞬間、φ が減じて逆起電力が減る。
そのため電流が増加して再び前と同じだけφができるまで電流が増加する。その結果は入力が増加するから引張力が増大し、その後漸次加速して釣合速度に至るまで加速する。その変化の模様の説明を4.13図に示す。 |
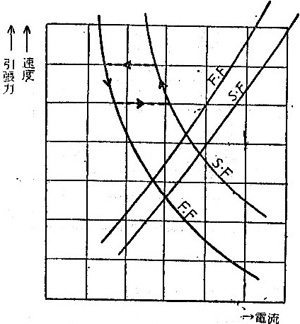
図4.13 電流と速度変化
|
一般に界磁制御率は全体の界磁アンペア・ターンに対して界磁制御を行った場合のアンペア・ターンの比の百分率を以って表わしている。
例えば40%の線輪を切り離しまたは分路した場合には60%の弱界磁と呼ぶが、在来の釣掛式電動機にあっては最大弱界磁率は60%が限度であった。これは閃絡の危険があったからである。
閃絡を防ぐには磁界分布を均等にするにあるが、直巻電動機では界磁と電機子とのアンペア回数比は常に一定だから磁界分布は均等で一般的には閃絡の心配はないといえる。
ただ弱界磁制御では磁界が歪んでくる。従って分路抵抗にインダクタンスを加えて急激の変化を避ける必要がある。
また最大の加速電流で補極が飽和しないことも必要である。
電動機の受ける衝撃は整流を阻害してこの閃絡の危険を誘発するが、釣掛式電動機の最大弱界磁率が60%を限度としたのも最近のバネ吊り式高速度電動機に較べて整流が悪い上に、外部からの衝挙がさらに閃絡を誘発する危険が多いことが主要原因であった。
パネ吊りされた最近の高速度電動機の弱界率は40〜50%まで許し得るに至ったので、SRPを大幅に増大するに至った。
すなわち弱い界磁で高速における出力低下を補い、スピード・レショを十分に活用して低速より高速に至るまで充分な力を発揮させて、所要のサービスが行えるようになった。
4.5.2 弱界磁定格 top
このように界磁制御の範囲が拡大され、スピ−ド・レショが大きくなり運転上の界磁制御の比重が増大してくると、界隔コイルの実効電流は一般に小さくなるので当然界磁巻線のスペースを割いて、電機子の容量増大に振り向ける設計が考慮される。
これがいわゆる、弱界磁定格の電動機であって、この種の電動機は全界磁状態でなくある程度の弱界磁の状態で定格を決定する。
ニューヨーク地下鉄新車用電動機WH−1447をはじめ最近の欧米の新しい設計は殆んど弱界磁定格であるのは実際使用状態に合致した合理的な定格といえる。
次に弱界磁は従来は電動機界磁コイルの中途からあらかじめタップを出して主界磁コイルの一部を切り離すか、あるいは界磁を抵抗をもって分路する方法によっていたが、最近の高速度電動機は抵抗とインダクタンスによって分路するいわゆる誘導分路によっている。
このような分路法による弱界磁制御には次のような利点がある。
(1) 快適な乗心地と高加速度・高速度という運転上の要求から制御袋置は20段程度の多段式から100段程度の超多段式まで使用されるに至り、弱界磁制御は電気車の起動のときと力行運転の高速のとき、あるいは電気プレーキのときの弱界磁遮断などと弱界磁の利用が広くなった。
弱界磁起動は起動トルクが小さくなるので衝撃のない滑らかな起動ができるためであり、弱界磁遮断は電気プレ−キのとき電気車の高速より常用発電ブレーキを適用すれば回路電圧が高くなり、途中ノッチで回路遮断とした時、衝撃があるので弱界磁することによってブレーキ力を減じて回路遮断をするもので、何れも快適な乗心地をねらった方法である。
このような用途に対しては弱界磁の制御段数は3段程度から4段とするのが普通であるが、誘導分路の分路抵抗からタップをとれば多数のタップが自由に選択出来る。
(2) 多数のタップを電動機の界磁から直接とり出すと、タップのために界磁の寸法が増大し電動機の小型化に逆行する。
(3) 界磁制御の段数に関係なく電動機の標準化が出来る。
なお誘導分路のインダクタンスの設計は主界磁の自己インダクタンスおよび相互インダクタンスと等しい値に設計するのを理想とする。
分路法による弱界磁のツナギ例を4.14図に示し、誘導分路の一例を4.15図に示す。 |
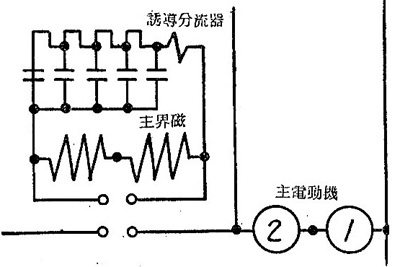
4.14図 分路法による弱界磁つなぎの一例
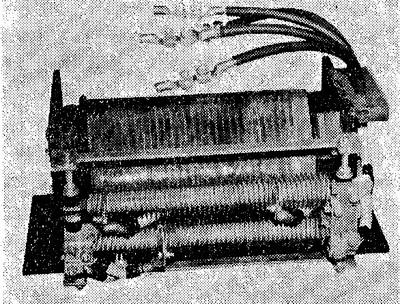
4.15図 誘導分路器
|
4.6 絶縁材料の進歩 top
4.6.1 完全B種絶縁
絶縁材料および絶縁処理法は過去10年間に格段の進歩をきたし、導体絶縁・スロット絶縁・テープ類は薄くなったばかりでなく、誘電体的ならびに機械的強度を増大して高温度に耐えることとなった。
また絶縁ワニスと絶縁処理法の進歩によって巻線の対地に対する強度は格段に増強されたのである。
一般に電動機のサイズは絶縁物の厚さによって著しく影響されるが、厚い絶縁物は、必要とする銅と鉄とのスペースを横取りするため、勢い寸法の増大を来たすばかりでなく、巻線中の熱損失の放散に対し大きな抵抗となる欠点がある。
最近の高速度電動機においては、A種の絶縁物は完全に用いられなくなったばかりでなく、従来B種絶縁の補助材として使用されていた木綿・紙などの有機質繊維類を大部分駆逐して、ガラス繊維で置きかえアスベスト・マイカなどとともに無機質絶縁物を用いている。
接着剤および処理用ワニスには従来のシェラック・ワニスを駆逐して、フェノリック・アルキッド系の合成樹脂――速乾性コイルワニス――を主成分とするものを主として用いる、いわゆる完全B種絶縁が電動機絶縁の標準となった。
このようなワニス類の性能としては、強さ・硬さ・軟化温度・電気的性質および熱処理温度・時間などが考慮されねばならないが、従来は主として、セラック・エステルゴム・コーバル・アスファルト・ギルソナイト・桐油・亜麻仁油・揮発油などを適宜の方法で溶解あるいは融合して所要の性質を出す油性ワニスが主体で、乾燥温度も110℃位であり、重合が緩慢であるので容易に固まらず、使用中高温度になると軟化し易い欠点があった。
これに反して、フェノリック・アルキッド系樹脂はアルキルフェノールをホルマリンと反応させた油溶性フェノール樹脂を乾性油と配合したフェノール樹脂ワニス、あるいはフタール酸、アジピン酸などを用いたアルキッド樹脂ワニスで熱硬化性があって乾燥速度も早く、乾燥皮膜は強靭で使用中の温度上昇で軟化することがなく、またスチロール・アルキッド系樹脂のワニスは不飽和ポリエステル樹脂をスチレン・ビニルトルエン・ジアリルフタレートなどの重合性溶剤に溶した樹脂であって、いわゆる無溶剤ワニスの形で、コイルを処理することが出来るからコイルに適度のしなやかさを持たせながら、しかも軟化流出する恐れがない特長を持っている。
これも乾燥速度、内部乾燥性がすぐれている。
シェラックは元来、アジアのインドなどに生育するアカシアの木に寄生するかいがらむし科に属する小さな昆虫の排せつ物である。
従ってシェラックの品質は昆虫の種類、その昆虫の育った気候・雨量・山の高度その他の天然的環境に支配され、不均一性を持った原始的絶縁物である。
従って苛酷な仕様の要求される電鉄用電動機の絶縁物としては不満足極わまるもので早くから信頼できる合成化学の産物が要望されてきた。
最近の合成化学の進歩は遂に目覚しい合成樹脂を次々と生みつつあり、絶縁ワニスの様相を一変するに至った。
4.6.2 H種絶縁 top
シリコンワニスは現在の絶縁ワニス中で最高の耐熱性を有し、耐水性も良好なため、H種絶縁ワニスとしてコイル含浸用・ガラスクロース用・ガラス巻線用・接着用・積層用など広く使用されるようになった。
シリコン(Silicon)とは含珪素有機化合物に冠せられたアメリカにおける総名称であって、日本においては珪素樹脂の呼称によって知られている。
このシリコンの本質的な特長は、その化合構造がSi−O−Siなる基本要素にメチル・エチルあるいはフェニールなどの有機基が結合している点であって、前者によってこの材料の耐熱性・絶縁性、あるいは機械的強度が得られ、後者によって耐水性・可塑性が付与される。
さらにこの基本要素を適当な数だけ所定の構造に重合することによって、シリコンの性状は液状・ワニス・樹脂・グリース、あるいはゴム状などと種々な形となる。
シリコンは前世紀の末期、ドイツにおいて初めて研究され引続いてF.S.Kipping(英)、E.G.Rochow、J.F.Hyde(米)などによって新分野が開拓されて戦時中および戦後米国において極めて著るしい発達と実用が見られている。
現在アメリカにおいては、Dow-Corning社とGEとが主として製造し、日本においても東芝・信越化学などが製造を始めている。
シリコンの共通した一般的特長は熱的に極めて安定で耐熱性に富み、化学的に不活性で酸化せず水分・湿気をはじく性質があり、電気絶縁性を有することなどである。
シリコン・ワニスは種々のアルキルシラン類を適当に配合し、加水分解して得られたアルキルシラノールを縮合させ、キシレン・トルエンなどに溶解してワニスとしたものである。
故にこの配合比や加水分解の条件、縮合の方法によって生成したワニスの性質が異なるので各使用目的に応じたものを選択する必要がある。
シラスチック(Silastics)と云う商品名で邱られたゴム状シリコンは特に広い温度、例えば−50℃から+130℃の範囲でゴム状を呈し、ガラステープと組合せたシラスチックテープは界磁などの外装絶縁に用いられ、シラスチックコンパンドも界磁絶縁に用いられる。
シリコン・ワニスとしては前述の通りシリコン単量体をトルエンなどの溶剤に溶かし、これを刷毛塗・浸漬塗などの絶縁処理、雲母その他の貼付、硝子織布を基材にした絶縁布の製作などに使用し、さらに表面の防火・防湿仕上用として適している。
焼付乾燥温度は約200℃を要し、従って紙・布などの有機質材料と200℃の併用は不可能である。
こうして得られたワニス皮膜は耐熱性・耐湿性に富み、従来もっとも優れたフェノリック・アルキッド系の合成樹脂ワニスも遠くこれに及ばない。
4.16図はこれらワニス皮膜の耐熱屈曲特性を示したもので、これは皮膜を所定の温度で加熱し、直径1/8インチに屈曲し、クラックの生ずる迄の時間を比較したものである。4.17図は在来のB種絶縁コイルとシリコン絶縁コイルの耐湿性を比較したもので水中浸漬時間と絶縁抵抗との関係を示している。
4.16図 シリコン・ワニスおよび
フェノールアルキッドワニスの耐熱
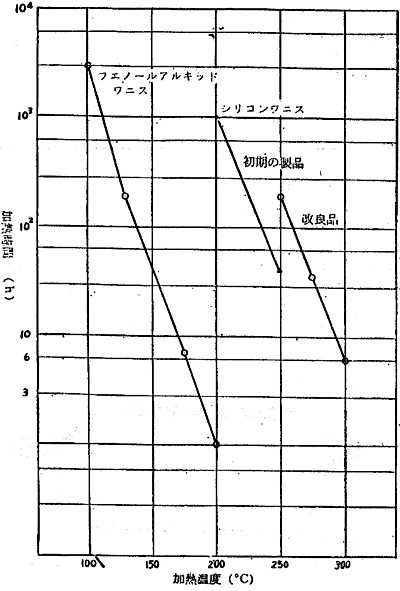 |
4.17図 シリコン絶縁コイルの耐熱特性
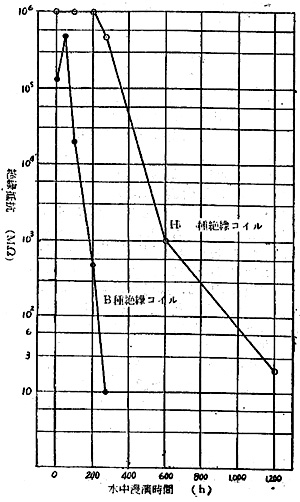 |
シリコン・ワニスの出現は絶縁物の耐熱度を飛躍的に高め180℃の温度上昇を許すH種の絶縁を可能にした。
しかしながら現状において価格が高いことと乾燥温度が高くて絶縁処理がやや困難なのでアメリカでも特別の用途のみに使われている。
完全にH種絶縁を施した電車電動機はアメリカにおいても、イギリスにおいても試験的に使用されている程度であり、全面的ではない。
また日本においても全面的でないようであって、現状は界磁絶縁には完全にH種絶縁が可能となったが電機子絶縁では完全B種の主絶縁の中に特に必要なところに部分的に使用する程度である。
その理由は180℃の温度上昇に耐えるシリコン樹脂に見合うべき他の部分の材質が劣るがためである。
例えば界磁の絶縁はH種になし得ても、電機子のライザー部の高温半田に問題があってH種の許し得る温度上昇に耐える完全な半田が得られなかったり、あるいは得られたとしても半田揚げの処運法になお研究の余地がある。
従ってシリコン樹脂の長所を充分に生かして完全にH種の電動機を製作するには一部の金属材料の研究が今後の宿題として残されている。
4.2表はシリコン2次製品比較の一例を示し、4.3表はB種との絶縁仕様の比較を示す。
なお、幾つかの新しい樹脂はすぐれたフィルム成型性をもち、電気的・機械的性質の秀れたフィルム材料となったが、その一つにテフロンがある。
テフロンは Du.Pont社で完成、生産されている四弗化エチレン樹脂の商品名で−73℃から+260℃の広い温度範囲にわたって使用でき、また最高の耐薬品性、優秀な電気特性を持ち、吸湿率も極わめて小さく、不燃性で機械的にも強靭である。
テフロンは非常に薄いフィルム材料とすることができ0.006〜0.05mmが市販されている。
電機子巻線のコイルの被覆、特に電機子鉄心のスロットの出口におけるコイルの放縦に用いる。(4.18図、4.4表参照)
4.5表は電動機の絶縁として実際に使用しているH種併用のB種絶縁材料表を示す。 |
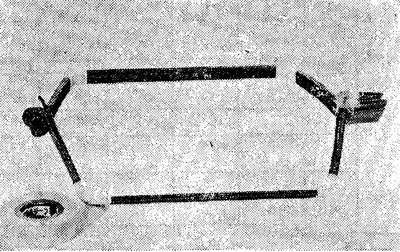
4.18図 電機子コイルのテフロン巻
|
4.7 炭素ブラシ top
4.7.1炭素ブラシの特性
いわゆる金属ブラシに対して炭素ブラシと一般に呼ばれる品種の中にも天然黒鉛質・炭素質および電気黒鉛質の3種がある。
この中で天然黒鉛質は非常に軟質で脆弱であり、また炭素質は摩擦係数が高く整流子周速の高いものには耐えぬため、電気車用の電動機にはこの両種のものは殆んど使用されていない。
現在内外において広く使用され、また研究の対象となっているものは、すべて電気黒鉛質である。
電気黒鉛質の中にも使用原料によって二つの品種があることは周知の如くで、一つは石油ピッチコークスあるいは石炭ピッチコークスを主原料とするいわゆるコークス系で、他の一つは油煙あるいはカーボンブラックを主原料とするいわゆるスート系に属するものである。
この両者は外観上全く異る色沢を呈し、固有抵抗・真比重などの物理的特性値に、著しい差異が認められる。
一例として有孔率と固有抵抗との関係を示したのが4.19図である。 |
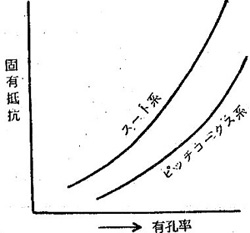
4.19図 有孔率と固有抵抗の関係
|
しかしながら電気車電動機用炭素ブラシの具備すべき必要条件の主なものは、激烈な衝撃振動に耐えるに十分な機械的強度、良好な整流を行うに必要な電気的性能であって、固有抵抗とか真比重などの個々の物理的特性そのものではない。
従って上記の条件を満足するものならば、ピッチコークス系に属するものでも、スート系のものでも充分に使用できるわけて、現に内外における電気車電動機用炭素ブラシとして賞用されているものに、コークス系とスート系のあることによって明白である。
さて実際にその選択に当っては、当然機械的強度と電気的性能に重点をおくべきことは上述の通りであるが、それぞれ関連のある諸因子との大略の関連を表示すると4.6表のようになる。
以下、ブラシ選択に当り注目すべき代表的な特性について考察してみることにする。
(1) 外観
プラシの初めから亀裂が入っていれば、これを |
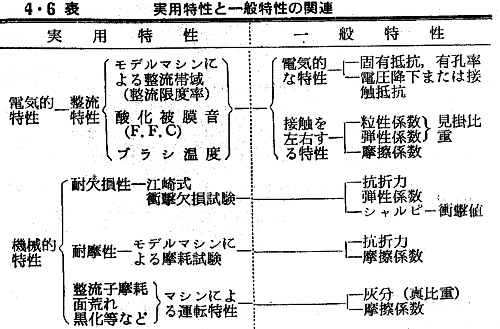 |
電喰を少なくするためには、プラシにピグテールを取付けることが推奨され、また塵埃防止には電動機風取入口に適当なフィルタ一を収付けて塵埃が直接ブラシ支え廻りに行かない構造にしている。
現車の電動機において、走行中どれほどの電流がブラシとブラシ箱内面との間に流れているかということを知るために最近、近鉄と筆者などとの協同研究により近鉄・奈良線において現車試験を行った結果によると釣掛式電動機で、ピグテール無しの場合と台車装荷式電動機でピグテール付の場合と比較して、前者の場合は100→500Aまで電流増加につれて側面に流れる電流の割合が約30→70%へ増加するが、後者の場合は電流の変化従って速度変化にかかわらず、約 O〜8%と殆んど一定の割合を示した。
この結果からみて明らかなように、振動衝撃のはげしい釣掛式電動機では、プラシとブラシ支えとの振動も大きく側面への電流が大きいために、ブラシ側面の電喰は生じて異常摩耗にまで進展する場合があることが明らかとなり、ブラシにピグテールをつけることは絶対に必要であり、台車装荷方式などの分離駆動式電動機においても、もちろんピグテールは取付けることが望ましい。
またプラシバネに電流が流れて、バネを鈍したりすることもあるので、この点からもピグテール付きとする方が良い。
4.7.3 分割型ブラシ
最近の高速度電動機用ブラシの顕著な特長として、2つの部分に分割された分割型のブラシが広く用いられるようになった。
これは各々の半分は、同じ材質の固形ブラシからできていて、両部の接触面の接触抵抗が整流改善に役立つこと、および互に分割されることにより質量が小さいので、特に高速の場合に整流子面によく沿って非常に緊密な接触を保持することができる結果、良好な整流作用が行われるとlいう利点がある。(4.26図) |
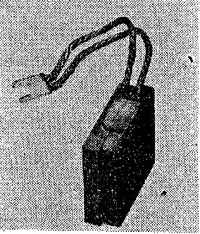
4.26図 分割型ブラシ
|
4.8 機械的設計の進歩 top
電動機の高速化は必然的に機械的設計の進歩、構造の改良となり、従来の釣掛式の構造とは完全に様相を変えている。
殊に機械的設計の特色は高速度を許し得るに足る次の
@ 整流子構造
A 整流子側端蓋を溶接一体とした丸形溶接磁気枠構造
にある。
この構造にすると整流子側端蓋が磁気枠の一部をなしているので正常な軸受けとブラシ支えの取付が保証できるからである。
4.27図は代表的高速度電動機の断面図の一例である。
4.8.1 整流子の構造 top
(1) アーチ・バウンド |
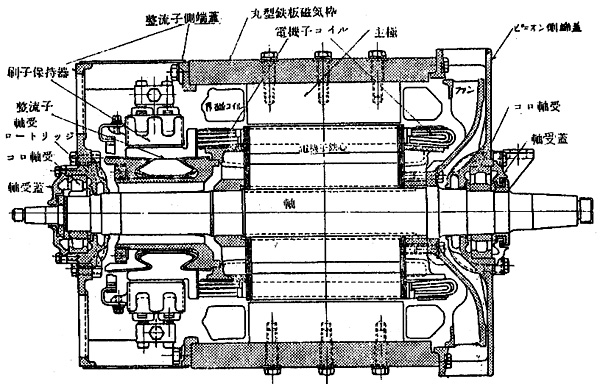 |
電動機に高速度が許せるに至った電機子構造上の大きな進歩は整流子にある。
100HP級の電動機が4,000〜4,500rpmの高速度で回転している場合、整流子片には遠心力として40〜50tという大きな力が作用する。
従って運転中の高速・高温による強大な遠心力および熱応力によって整流子が変形して火花の原因とならないよう、材料および工作には特別の注意が必要である。
整流子は多数の模型の硬銅整流子片と、これと同数のセグメント・マイカの薄板とを交互に重ね合せて、円筒型に丸めて軸方から鋼の整流子おさえ用リングで締付けるのであるが、このセグメント・マイカ板は多数の剥がしマイカを接着剤で数10層も張合わせたものであるから、熱的・機械的に充分強靭なものではない。
従って熱膨張係数も異なり、弾性係数も異なる。これら多数の銅片と絶縁物からなる整流子が100℃を越える温度となり、高速回転し、かつレールからの振動衝撃を受けるという悪条件のもとで、その整流子面を常に平滑に保持することは容易なことではない。
殊に高速度電動機となると整流子の周速は60m/sにも速するので整流子が電動機の死命を制することとなる。
整流子の締付構造は従来はVバウンド(4.28図)と称する整流片を軸方向に締付ける方法が専ら行われていた。
この方法では軸方向に締付ける平行分力と整流子中心に向って締付ける垂直分力のほか、僅かながら遠心分力が作用する。 |
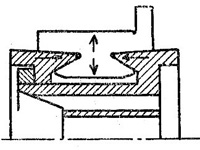
4.28図 Vバウンド
|
すなわち、軸方向には締るが肝心の垂直方向には充分締らない欠点があった。
まして長年、使用して高温・冷温の熱サイクルを繰返すうちに、セグメント・マイカやVマイカの接着剤が枯れるため、さらに締付けを行っても、V部分の上の端が天井づかえして、かえって整流子片を押し上げるように締付けられ、無闇に締付けると、遂には整流子片を永久変形させてしまう結果となる。
従って上記のような巨大な遠心力を受けるには極めて不安な構造であった。
しかるに最近、専ら採用されているアーチ・バウンド方式(4.29図)の締付構造によると、整流子おさえの上部と整流子片との間に隙を持たせ、専ら30°の部分で完全に締付けて遠心力に対抗する方式で締付けの遠心方向の分力はゼロとなり、整流子片を中心方向に引込むように締付けるために高速度電動機用整流子として万全の構造となった。 |
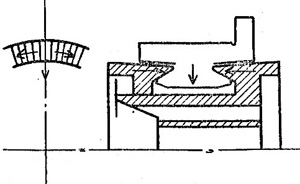
4.29図 アーチ・バウンド
|
(2) 整流子面の機械的状態
整流子の使命はブラシと常に正常に接触することである。
接触電圧降下は、ある程度の変動は差支えないが、ときにはそれ程ひどく悪い火花を発生しないにも拘らず電流を整流子片に流すことのできないような整流子面の状態になることがある。
このような状態ではもちろん、満足な整流を行うことはできなくなる。
30m/s以上周速の整流子面はブラシが整流子片全部に均一に接触するためには非常に平滑でなければならない。
整流子片は遠心力と温度とによって半径方向に変形する。
これらの整流子片は絶縁物のセグメント・マイカによって絶縁する必要があるから、整流子片の1枚1枚は不均一に変形する。
隣同志の整流子片が不均一に変形を超すと、整流子面は凸凹の面となる。
整流子面の変形の影響を考えて見ると、偏心と上記の隣同志の整流子片の凹凸――いわゆる、ハイバー(high bar)――とは区別しなければならない。
普通偏心は3/100mm程度であれば、整流子片とブラシ間では接触しないことはないが、ハイバーは極く僅かでも両者が接触しない場含が生じる。
例えば4.30図のように、1枚の整流子片が隣りの整滋子片よりも低ければ、ブラシは普通2〜3枚の整流子片と接触するような厚みになっているから、この低い整流子片とは接触することができない。
また、4.31図のように1枚の整流子片が隣りのものより高いと、ブラシはこの整流子片にぶつかって跳り上る。
その跳り上がる程度は周速の高いほど、大きくなる。 |
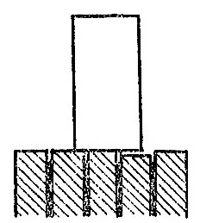 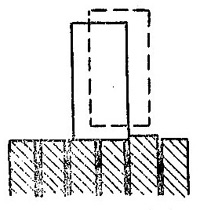
4.30図 ローバー 4.31図 ハイバー
|
このハイバーの程度がどの程度になればブラシが整直子から離れるかについて実験上確めてみた。
測定回路は4.32図に示す如くで、250溝の模擬整流子に任意の高さに調整できる整流子片を作り、これによるブラシの振動状態を電磁オシログラフで電圧降下法で観測した。
調整する整流子片は片の下に錫箔を敷いて高さを約2/1,000〜20/1,000mmまで調整した。
実際の整流子を使用すると速度と温度によって徴妙に変化するものであるから、たとえ試験前にダイアルインディケーター(dial indicater)で凹凸を測定してハイバーの量を出しても、運転中どれだけになっているか判らないから、試験に使用した整流子はセグメント・マイカの入らない一体のものに溝を切ったものを使用した。 |
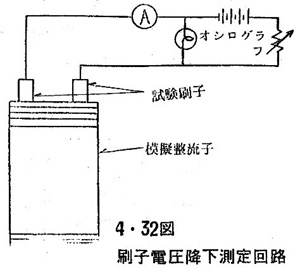 |
ブラシ電圧降下のオシログラフに現われた波形の一例を示すと4.33図の如くで低圧スケールの左側は正常なブラシの接触を示し、右側はブラシが、ハイバーによって跳躍して整流子から離れた状態を示している。
この結果からブラシが整流子面から跳躍するハイバーの程度は5/1,000mmで全く跳躍を生じない限度としては3/1,000mmであることがわかった。 |
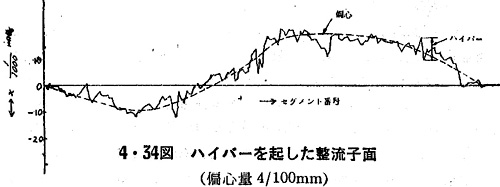 |
(3) ハイバーの原因
上述の如く、ハイバーの量が5/1,000mm以上の場合には非常に有害な火花を生じるものであることが判明したが、さてその原因は何であるかについては理論的に解明することはかなり厄介である。
それは整流子の構造が前に述べたようにその構成材である整流子片・セグメントマイカ、およびスパイダー・クランパーなどの整流子おさえがすべて遠心力と熱応力に対して弾性限内の応力を受けて、その変形が弾性変形であれば組立圧力で何ら問題は起らない訳である。
しかるにセグメントマイカとVマイカは完全弾性の性質から欠けている。
従来使用して来たマイカ接着剤のシェラックでは圧縮強度が比較的小さくて、Vマイカの接触圧力は使用状態の熱応力でこの限度を超過して破壊される場合がある。
次に考えられる原因としてセグメントマイカのクリ−プ特性がある。
金属材料でも高温高応力の状態ではかなりのクリープが起きるものであって、ましてシェラックなどの樹脂で張り合せたものでは、この性質がはなはだしいものと考えられる。
かかる状態を繰返すことによって、セグメントマイカは徐々にやせて弾性を失って行き、これに対してスパイダー・クランパーが殆んど剛体と見なせる状態にあるから、組立圧力は減少して、整流子片の側圧を減少させ、遂には遠心力による飛出しを防止できなくなり、ハイバーをおこすものと考えられる。
このようにしてできたハイバーの静止冷温時に、ダイアル・インディケーターで測定したものの一例を4.34図に示す。
ハイバーの測定はブラシとの摺動面以外で行わないと整流子自体の本当のハイバー量が判らないから注意を要する。
運転中ではこの形状はたえず変化して、あたかも、呼吸作用をする生物の如き状態にあるものと考えられる。
(4) 生きた整流子
前述の如く整流子の構成材である、整流子片・セグメントマイカ・Vマイカ・スバイダー・クランバーなどが電気車の運転時の遠心力と熱応力を受けて膨張・収縮を繰返しても互に親密性を維持して常に弾性を保持できれば、整流子面は常に平滑に保たれブラシとの良好な接触を保持して、火花の出ない整流作用を行うことができる。
従来のセグメントマイカ・Vマイカの接着用ボンドとして使用されて来たシェラックはすでに現在のような高速度電動機には不向きとなり、これに代るものとしてアルキッド系およびビニール系の合成樹脂が接着に使用されるに至って従来のシェラックのものに較べて強度が増し、高温においての安定性も良くなった。
整流子片は高温においてクリープしないよう含銀整流子片とし、寸法精度もはるかに厳格となっている。
整流子おさえは熱処理を行った強度の大きい鍛鋼製を使用するが遠心力および熱応力に対して、あらゆる方面から強度計算を行って強固なものとしているので高速度電動機用整流子の構造部分は一見不必要と思われる程大きく見えるのはこのためである。
整流子のシーズニング(Seasoning)は最高運転速度の120%の速度と高温において充分行う必要がある。
高速度電動機の生命はまさに整流子にある。
整流子周速の限界が高速度電動機の許容最高回転数の重要な要素であり高速度化の限界である。
SRPも小型軽量化も上述の如く、高速・高温において安定する生きた整流子が作れるようになって達せられることになった。
4.8.2 磁気枠 top
丸形の鉄板溶接構造が従来の釣掛式の角形鋳鋼に取替った。
鉄板溶接によって製作が簡単になって製作費の原価低減となったばかりでなく、磁気回路としても鋳物よりも磁気抵抗が減少したこと、材質の不均一、かくれた鋳巣などによる磁気回路の不均一がなくなったため、磁気特性が良好になったほか、磁気枠の所要断面積も小さくて済み、同一設計にもかかわらず従来避け得らわなかった回転数の不均一という欠点がなくなった。
高速度電動機となって、電機子直径が小さくなったのに比例して、磁気枠直径も小さくなるので、2重の重量軽減となったばかりでなく、磁気回路の磁路長が短くなって、同一磁束に対しては、所要の界磁巻数が少くてすむという結果にもなった。
丸形磁気枠では界磁コイルの占積率が悪くなるというのが一般常識であるが4.35図の如く、コイルは磁気枠に沿って曲げ、しかも主極コイルと補極コイルが競合するところは機械的に削り落すことが行われる。
銅線は熱伝導率か良いので局部加熱はさほど心配はない。
むしろ従来のセメント充填は熱放散が阻害されるので好ましくない。 |
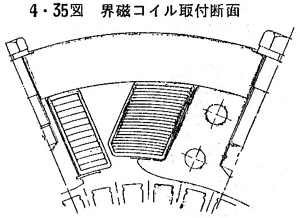
|
4.8.3 界磁コイルバネ top
釣掛式電動機の界磁コイルは強固なコイル固定用バネによって磁気枠と磁極片部との間に締付けて取付けられ、振動衝撃から保護する構造であった。
電動機がバネ吊りとなって、これらのレール面からの振動衝撃から開放されるに至った結果、一般には界磁コイルバネは不必要となって界磁コイルは磁極片部の平ワッシャーと磁気枠との間に固定して取付けられる簡単な構造となった。
4.8.4 電動機口出線 top
電動機には電機子に2本、主極に2本、合計4本の口出線が出ている。弱め界徴用として従来の釣掛式では界磁タップのための口出線がさらに必要であったが、最近の高速度電動機では弱め界磁は分路法によって主極の口出線間に誘導分路器を接続する方式であるため、弱め界磁のための口出しは必要としない。口出線は従来用いられて来た天然ゴム絶縁と編組塗料からなる構造のものは耐熱、耐燃などの点で完全B種あるいはH種の電動機と絶縁協調がなり立たず使用できない。従って最近の口出線は外部編組・塗料の代りに塩化ビニールまたはクロロブレンなどの新合成材料を用いたものや、アメリカの Du.Pont
社の開発した、商品名ネオプレーレン(4.36図)という合成ゴムが登場している。 |
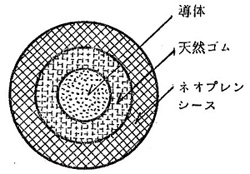 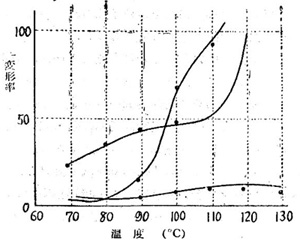
4.36図 ネオプレンシース口出線 4.37図 ネオプレン口出線の熱変形試験
|
ネオノレーンはアセチレンガスと塩酸ガスとによって合成された薄クリーム色のゴムようの弾力のある重合物であって、実際使用に当っては、ゴム工場で生ゴムとほぽ同じような方法で加工される。
天然ゴム製品と較べてネオプレーン製品の特長は
@ 油に対して強いこと
機械油・絶縁油・グリースなどの多くの油に対してほとんど侵されない。
A 日光・オゾン・酸化・熱などに耐えて老化し難いこと。
耐老化性については、例えば100℃のギヤー老化試験の結果は4.7表の通りである。 |
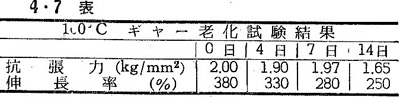
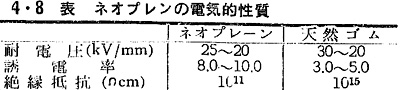 |
熱変形試験の結果は他のビニール系の材料と異って高温において軟化しない。
4.37図は1cm平方当り22kgの荷重を加え2時間後の高さの変化を求めたものである。
耐寒性については−50℃程度まで使用可能である。
B 燃え難いこと。
点火しても焔を取去ればそのまま消化し、決して延焼しない。
C 耐酸性の強いこと。
電気的性質については右上の4.8表の通り、天然ゴムに劣る。
以上の如く、ネオブレーンは耐久性が擾秀であるので外部シースの保護層として使用されている。
PCC用の電動機では磁気枠から絶縁された3本の絶縁スタッド形の口出しターミナルが使用されている。
ターミナルは真鍮製で、テーパーが付けてあり、3本のうちの中央のスタッドボルトはクランプ用である。
これは電動機の限られたスペースで、ターミナルの取外し、取付けが便で簡単である。(4.38図、4.39図) |
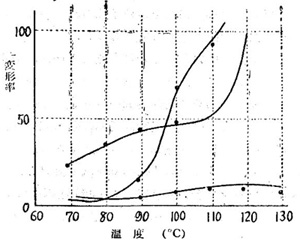
4.37図 ネオプレン口出線の熱変形試験
|
4.34図 PCCカー用電動機の絶縁スタッド形
口出線ターミナル
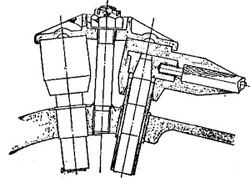 |
4.39図 PCCカー用電動機
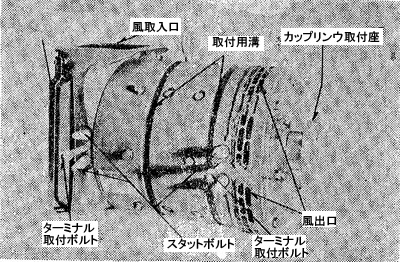 |
4.8.5 整流子側端蓋及び送風ファン端蓋
整流子側端蓋は磁気枠に溶接してあるので軸受およびプラシ支えの位置が正確に保たれる。
送風ファン側端蓋はフレーム、ボアにはめあわされた取外し可能の鋳鋼製である。
両端蓋とも軸受を内蔵しているが整流子側端蓋にはブラシ支えが取付けられ冷却空気取入用の口が開けてある。
ファン側の端蓋には排気口があけてある。冷却用空気は一方は界磁と電機子表面の間のスペースを通路とし他方は電機子コアーの通風溝を通って並列通風としてファンによって吸出されている。
4.8.6 電機子転り軸受 top
(1) 転り軸受の利点
旧式の電動機の軸受はウェィスト、給油式滑り軸受(Waste, Packed Sleeve Bearing)であったが高速度電動機ではグリース給油式転り軸受である。
転り軸受が滑り軸受と較べて、摩擦抵抗を減じ、起動の際のトルク損失を減ずることは、むしろ副産物であって、転り軸受には次の3つの利益がある。
@ 高速度において潤滑が簡単でしかも信頼度が高い。
A 軸方向に軸受けの占める長さが短くてよい。
B 滑り軸受のような摩耗がないので、歯車中心距離が正確に保持される。
C グリース潤滑剤であるので、オイルのように漏油と蒸発がなく補給の手数がほとんど不要である。
高速度電動機のこれらの転り軸受は
a ファン側……端蓋の中に嵌入されている。
b 整流子側……別のカートリッジの中に嵌入されてさらにこのカートリッジが端蓋に取付られている。
整流子側の軸受はスラスト止のコロ軸受かまたはラジァル玉軸受で電機子軸方向に嵌め合わされている。
ファン側の軸受は重負荷や衝撃荷重がかかるのでフリー形のコロ軸受を使用する。この構造方式の主要な利点は軸受を取付けたままで電機子の取外しができることで、軸受を汚すことがない。
このような取外しは整流子端蓋にカートリッジを支えているボルトを取外し、さらにファン側の端蓋をフレームに支えているボルトを取外せば良い。
ファン側の端蓋と整流子側のカートリッジを取付けたまま、抜出した電機子の写真を4・40図に示す。
このような構造故に整流子面の削正に際しては電機子を抜出して、簡単な取付具に自己の軸受を支えとして利用できるという便利さもある。 |
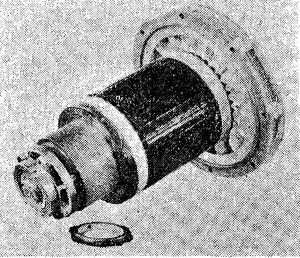
4.40図 カートリッジ形電機子
|
(2) 速度に対する選定上の注意
軸受の許容速度は原則として熱の発生によって制限されるが、その熱の発生は回転時の摩擦によるものであるから、結局この摩擦が軸受の許容速度を決定する要素となる。
従って摩耗の少ないラジアル玉軸受やコロ軸受は高速度に適する。
この許容速度は潤滑剤の量、質および潤滑法にも大いに関係をもち、保持器の材質および設計にも関係する。
@ dn の値
軸受の限界速度を決定する要素はいろいろあり、明確にこれを決めることは困難であるが、一般にはその限界の基本を軸の回転数、n・rpm と軸受の内径 d・mm との相乗積にとるのが便利である。
与えられた軸受形式・使用潤滑剤・潤滑方法などでいろいろな限界値が経験的にきめられているが、最近の高速度電動機の dn は概略
4.9表のような数値となり、30×10の4乗の前後となっている。
中空軸方式の電動機の例では4.10表の数字となる。
dn の値が30×10の4乗を超過する仕様に対しては、材質・精度・グリースの質および潤滑法に特に注意を要し逐年上昇しつつある高速度電動機の許容最大回転数は、転り軸受の許容速度によって制限を受ける段階にまで達しつつあることは、シカゴ地下鉄の100HP、6,500rpmの新形高速度電動機が良い例である。 |
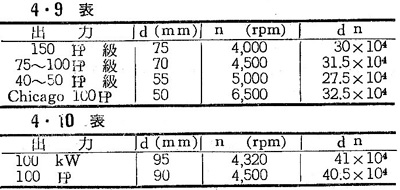 |
A 品質
電車用転り軸受は転動体がかなりの加速度と衝撃を受けるので、ラジアル遊隙の大きいものが要求され、保持器や転動体の遠心力あるいは慣性力を考慮して特別の設計のものが必要である。
従って品質については
a 内輪および外輪は全て鍛造品で土.質のものであること。
b コロは全てクラウンド.ローラを使用し、コロ材は特に上級の材料であること。
鋼球はJIS上級以上の高炭素クローム鋼球であること圈保持器材料は高力黄銅鋳物製材を使用し、外輪案内形とするdnが50×10の4乗以上の場合にはアームス・ブロンズ製材料を使用する。
B 精度
寸法精度・回転精度ともJIS上級であること。
C グリース
グリースは鉱油と石鹸とを主成分とする軟膏状の潤滑剤であるが、グリース種類の選択・稠度・補給周期・グリース注入量が問題になる点である。
a グリース種類
Ca−Na系、グリースに属する4.11表のものが、高速度電動機としては最も適当である。
シリコン・グリースは−73℃〜+200℃位までの広い適用温度を持つ、耐熱・耐冷グリースであるが、潤滑性能としてはあまり良くなく、一般には電車用としては使用されていない。 |
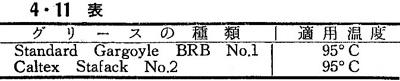 |
b 稠度(ちょうど)
各種グリースには柔いものと、硬いものとがあり、これを稠度番数で区別しており、普通 250位が適当である。
グリースの稠度は鉱油における粘度に相当するものでグリースは半固体であるために硬さで区別されている。
この硬さを表わすのが稠度であって規定の稠度計で測定する。
測定の方法は、試料のグリースも規定の円筒状の捏和(じょうわ)器に入れて、60回プランジャーを往復してグリースを捏和してから表面を平滑にして、真鍮製の円推を一定時間グリース中に貫入させる。
この貫入した深さで硬さを表示する。これが1/10mmの単位で稠度計の目盛に示されるのであって稠度250とは貫入円推が25mmの深さだけグリース中に貫入したことになる。
軟いグリース程、稠度の数値は多くなる。
グリースの稠度は原料鉱油の粘度よりも、石鹸の種類と量に多く関係し、なかんずく、石鹸の量に最も関係する。
またグリースを幾回も練ってゆくと段々軟かくなってくる。
このグリースが練られることによって稠度が変化することは石鹸のゲル化能によるものと考えられる。
もちろんこのように軟化したグリースも練捏を中止して放置すれば時間と共に、ゲル化してもとの調度に近い値に迄回復する。
転り軸受には練捏によって、あまり稠度の変化しないものが望ましく、SKFの指導書には速度系数が増大する程、硬いグリースを推奨している。
c グリース注入量
グリースの量が多くなると軸受温度が昇ってくる。
高速のもので特にこの影響が大きい。普通グリースのポヶット容積の1/3〜1/2が適当である。
d グリース補給量
グリースはある期間運転されてシャーを受けたり、温度が昇る場合には劣化するものと考えねばならない。
このために dn に応じて何時間位の運転をすれば、グリースの補給をすべきかを指定したものがSKFのグラフである。
すなわち繊細に軸受内径を取り縦軸に回転数を取り、この合致点を求めカーブ上の数字を読めば、これがグリース補給を要するまでの時間を表す。
なおこの線図を作るために使用されたグリースはSKF#28グリースであるが、リチウムグリースを使用すれば、この寿命時間を幾分増すと考えて良い。
4.41図および4.42図にこの関係を示す。
4.41図 グリース補給間隔(SKFラジカル、球軸受)
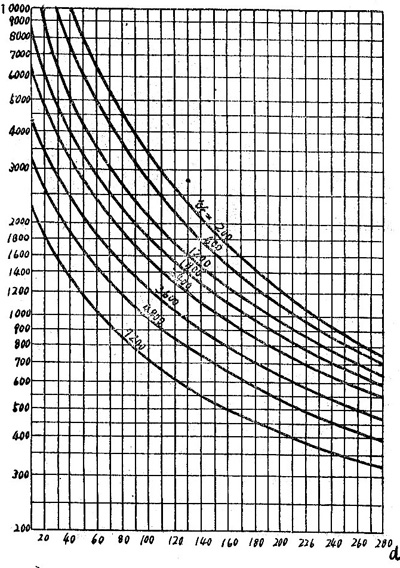 |
4.42図 グリース補給間隔(SKFコロ軸受)
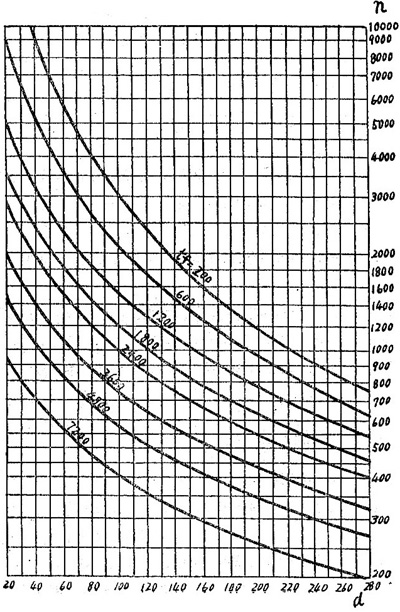 |
4.8.7 ブラシの位置とブラシ支え top
電機子巻線が波巻の場合には、ブラシの位置を必ずしも磁極の数と同じくする必要がないので、正・負 2ヵ所だけでも良い。
従って従来の電動機には点検の便を考慮して、4極の場合でもブラシ位置は正負 2ヵ所だけにする場合もあった。
この場合には一つのブラシ位置を流れる電流は、電動機の全電流となるので 4ブラシ位置の場合に較べてブラシの所要断面積が増大する。
整流子円周上のブラシ幅は整流作用上、ブラシカバーリングの制限を受けるので増大できないから、当然整流子軸方向のプラシの長さが増大する結果となり、整流子片の軸方面の長さが増大する。
その結果ブラシ位置が正・負 2ヵ所の場合の欠点と利点は次の通りである。
(1) 欠点
a 整流子が良くなって電動機の誤殺が増す
b 電機車電動機のうちで軌間の制限を受けて、電動機の軸方向の長さに限界のある電動機においては整流子寸法が長くなると、電動機出力に関係のある有効鉄心長 Lc が短くなって出力の低下となる。
ただし軌間が広くて出力に余裕のある場合にはこの限りでないことはもちろんである。
c 整流子が長くなるため、ブラシ接触点とブラシ支え取付位置との距離が延びて、電動機枠の振動が大きくブラシに伝達され、ブラシと整流子面との接触が悪くなるばかりでなく、ブラシ接触点が正確に保たれない。
これは整流子周速の増大する高速度電動機においては最も悪い影響を与える。
(2) 利点
a 整流子が良くなるので整流子の表面積は増加して熱放散が良くなり整流子の温度が低下する。
従ってブラシの温度上昇も多少低くなる。
b ブラシ位置が2ヵ所であるため点検に便である。
高速度電動機においては上記の通り電動機の小形、軽量化のためと、整流作用の良好のためにブラシ位置は磁極の数と同じくする。
ブラシ支えの取付は、いわゆるエンド・マウンチングで取付容易である。磁気枠と保持器を取付ける整流子側の端蓋は一体溶接構造で、電機子軸受を内蔵する構造であるため、電機子軸とブラシ支え支持点の関係位置が正確に保たれて整流子面とブラシとの接触が正確となる。
ブラシ支えの端蓋ヘの取付位置の高さはブラシ接触点にできるだけ接近した位置で支持しているので、一層ブラシ接触点が正確に保たれるという長所を持っている。
プラシの接触圧力調整バネも調整容易な構造となっている。
4.8.8 バインド線とクサビ top
電機子巻線は鉄心のスロットの中に収められ、従来は磁性鋼線でしばりつけていたが高速度電動機ではクサビによって保持されている。(4.43図)
非磁性鋼線が発達してからは電機子巻線のりアクタンス電圧を減少させ、従って整流作用を改善し、かつバインド線中、渦流による損失を軽減して、電動機出力を増大するために広く用いられるようになった。
しかし電機子回転数が段々高くなり、従ってコイルの遠心力が大きくなるにつれて、パインド線の必要量が増大し、遂には鉄心部においてはスロットのクサビで巻線を抑えることが必要となってきた。
クサビ構造はバインド線よりも高い周速において強度が大きく信頼度が高い。
このようなクサビを使えば、バインド線中の損失はなくなり、スロット内交叉磁束は減少するし、鉄心の歯部からの熱放散は良くなり整流作用は良好となり出力増大ともなる。
今日では最高許容回転速度における電機子の周速は、シカゴ地下鉄の100HP、最高6,500rpmの高速度電動機の場合、82m/sという驚異的な数字となっている。
クサビは一般には布入ベークライト製かガラス繊維、アスベストなどをワニスで処理し圧縮した強固なものが使用される。 |
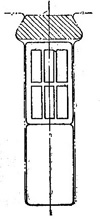
4.43図
電機子溝内のコイルとクサビ
|
4.8.9 フラッシュ・リング
架線電圧の急変による電動機の印加電圧急昇あるいはサージ電圧から整流子の閃絡を防ぐため、また閃絡の被害が軸受に及ぶのを防止するため4.44図のようなフラッシュ・リングを設けて電動機を保護する構造となったことは従来の釣掛式電動機に見られなかった進歩の一つである。
4.8.10 ファン
形状に工夫を払って通風効果を大にしている。
旧式の電動機ではファンの材質は鋳鋼または鉄板が普通であったが高速度電動機では高カアルミ合金を使用し軽量化の効果をあげている。(4.45図)
4.44図 フラッシュリング
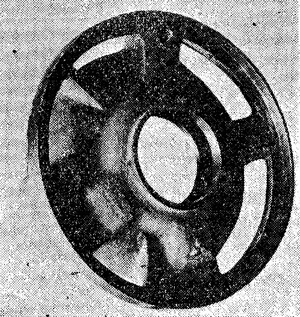 |
4.45図 ファン
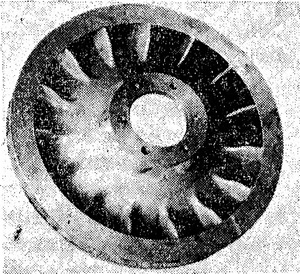 |
4.8.11 電機子の動的釣合 top
電機子の動的釣合は従来のような低速度電動機においてすら僅かの残存不釣合量も、大きな遠心力を受けて振動の原因となるので極めて重要な問題であった。
高速度電動機においては特に動的不釣合量は厳重に取除く必要があり、許容残存不釣合量は数グラム程度までとされている。一般に残存不釣合量によって生ずる遠心力の大きさは次式で与えられる。
F=5.6×Da nの2乗M×10の-2乗(kg)…………4.7式
F:遠心力(kg)、Da:電機子直径(cm)、n:rpm、M:電機子表面の残存不釣合量(g)
(4.7)式からDa=25qmの円周上に 1g の不釣合量が残存している電機子の場合、この高速度電動機が5,000rpmで回転したときの遠心力は 3.5kgとなる。
従って数グラムの不釣合量の場合はこれに数倍する遠心力を生ずる。
動的釣合には、精密な動的釣合機によって不釣合量を測定し、一般には釣合うウェイトは電機子のコイル端の支持金物のポケットに必要とする重量を埋込む構造となっている。
4.9 電気的設計の進歩 top
4.9.1 電動機の端子電圧
最近の高速度電動機の特長は、電動機の低端子電圧にあって、600Vの架線に対しては、300V瑞子電圧の電動機が2台永久直列に接続され、1,500Vの架線に対しては、375V端子電圧の電動機が4台、永久直列に接続される。
600Vの架線に対する300V瑞子電圧電動機の着想はすでに1925年頃、分離駆動方式試験時代のアメリカに実用されていた。
良好な整流作用のために、電動機設計上考慮すべき要点の一つは、低い整流子片間電圧に設計することであるが、整流子片数を大きく選ぶと整流子直径は大きくなり、整流子周速の増大となって良好な整流と矛盾する。
整流子周速の最大を安全範囲内に保ち得るよう整流子直径を小さくすると、整流子片数が小さくなり、整流子片間電圧が大きくなって閃絡の危険が増大する。300Vあるいは375Vの端子電圧の設計は、この整流子片間電圧を少くとも従来の600Vあるいは750Vの端子電圧の電動機と較べて 1/2 に下げることのできる有効適切な方法である。
また反面整流子片数の選択に余裕ができて、少い整流子片数とすることもできるので各整流手片は、より厚く、より丈夫に設計できることとなって結果的には高回転から生ずる大きな応力に充分耐える強固な整流子が得られることとなる。
300Vあるいは375V端子電圧の電動機の600Vあるいは750V端子電圧の電動機に勝る他の利点は、波巻の場合電機子導体が2倍の太さになし得ることである。
このことは電機子巻線が機械的に頑丈になり取扱いが楽になることでもある。
対地絶縁は300V端子電圧電動機は600Vの、また375V端子電圧電動機は1,500Vの絶縁が必要である。
すなわち架線側の電動機は対地に対し全架線電圧が印加されるからである。
4.9.2 電機子の設計 top
(1) 一般的傾向
電機子の設計は電機子導体の太さ・寸法・数およびスロットの数・寸法・スロット中の導体配置を選定することである。
整流・閃絡特性・温度上昇も電動機のサイズも重量も、これらのスロットの設計に密接に関係してくる。
電機子導体の絶縁は2重ガラス絶縁に変り、最近の進歩した絶縁材料、たとえば、ガラス繊維のテープ、ガラス布張りのマイカラッパーなどが電機子コイルの絶縁に使用されるようになって、スロットの導体占積効率も増加するし、熱放散もよくなった。
電動機が小形になったことと1回巻きになったことなどは一層電機子巻線を容易にしている。
高速度電動機の電機子の設計は一般的傾向として、整流子片数を整流子周速の許す限り、大きく選択して、電機子導体の全数を大きくする。
従ってスロットの数を多くするが、1個ののスロットの中に納める導体数を少くする。
前述の如く、整流子片の最小幅は機械的強度に制約されて限度がある。
従って整流子片数の増大は整流子直径の増大となり、整流子周辺の増大となるがこれはまたリアクタンス電圧の増大となって整流作用を阻害することになる。
そこで整流子片数にも最大の限度がある。
1回巻きであるので整流子片数は電機子全導体数の 1/2 となるが、この電機子全導体を電機子全表面に浅いスロットに納めて分散する。
その結果はスロツト内のアムペア・ターン数が小さいので発熱体が分散することとなり熱放散が良くなる。
従って、導体の電流密度を大きくできて導体寸法が小さくなる。
導体が細くなるので、コイル・エンドが短かくなって、リアクタンス電圧が小さくなり良好な整流が得られる。
コイル・エンドが短いことは、また有効鉄心長 Le が長くのばせることとなって、出力の増大となる。
電機子が高速度となると、周波数増加による導体内の渦流損も増大するので一般には丈の低い平角線が望ましい。
このことは発生する損失が誠少し、容量の増大となるが、整流作用の面からは丈の高い導体の方が好ましいという説もある。
それは整流作用が行われている間のエネルギー中の幾分かを火花としないで、導体内の熱に転換することができるので、導体内に渦流を生じて損失を増大するが、この渦流は却って整流作用を良好にする。
すなわち問題は整流作用の困難さと損失による熱とを天秤にかけて、どちらを選ぶかを個々の設計の場合に選択する必要がある。
電機子の通風量の増加、薄い最近の絶縁物の進歩による良好な熱放散および、電機子表面の導体分散による熱放散などによって、導体の電流密度は飛躍的に増大して来て従来の電動機では一般に4〜5A/mm平方であったが、最近の高速度電動機では6〜7A/mm平方となっている。
(2)波巻と重巻
従来、電機子巻線には波巻が採用されて来たが、300V〜375Vの低端子電圧の高速度電動機では重巻を採用して有利になる場合が多い。
一般に重巻はコイルの両コイル辺が相隣れる整流子片に接続され(4.46図)、波巻では約 2磁極ピッチ離れた2つの整流子片に接続される。(4.47図)
波巻は高圧小電流の電動機に適し、重巻は低圧大電流のものに適することは波巻が磁極の如何にかかわらず常に 2回路であるのに反し、重巻では磁極数と等しい内部回路数となることから衆知の通りである。 |
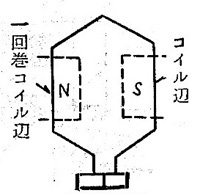 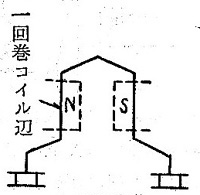
図4.46 1回巻の重巻 図4.47 1回巻の波巻
|
4.51図 電機子コイルと均圧コイル
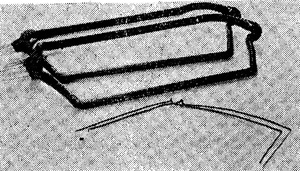 |
4.52図 波巻と重巻の電圧に対する出力の関係
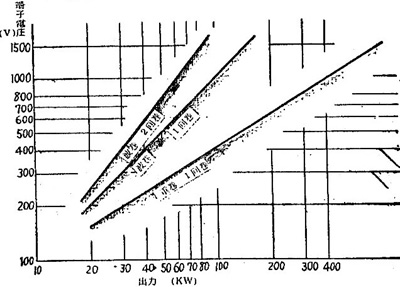 |
すなわちますます小馬力の高速度電動機で所要の運転性能が得られることとなり、この面からも電気車は小形軽量化される。
下の4.16表に従来の低速度電動機と最近の高速度電動機との連続定格電流と 1時間定格電流との実測値の比較を示す。
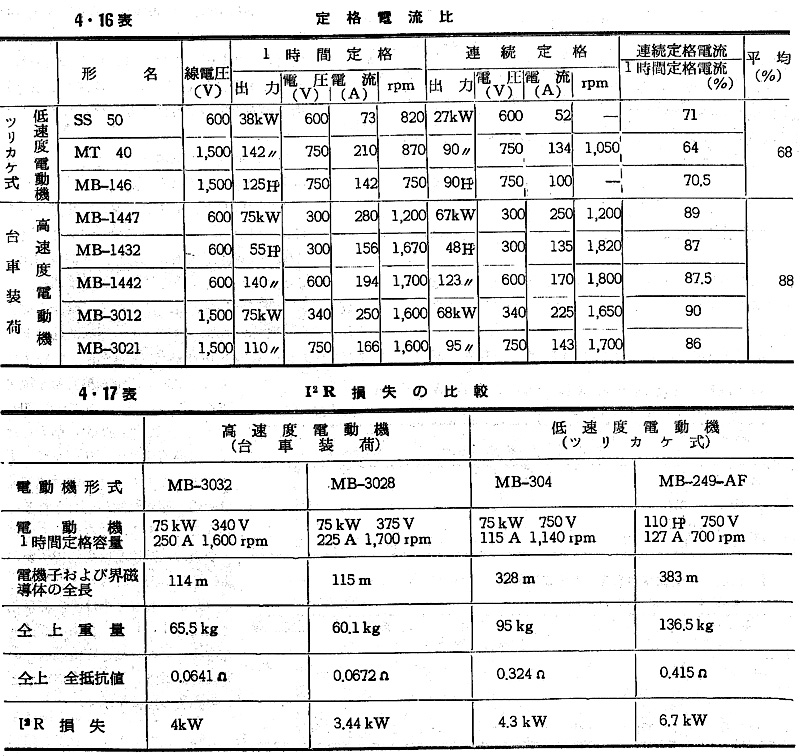
4.11 効率 top
高速度電動機は元来、低速度電動機より同じ電圧で同じ容量のものを比較した場合効率が高い。
これは電機子および界磁の巻線の導体致が少い上に短いことが主要な理由である。
100HPの高速度電動機と低速度電動機についてこの関係を比較すると上の4.17表となる。
高速度電動機は” I2乗R損失”が少い上に特に高加速度の負荷の場合に、この影響が顕著である。
鉄損と摩擦損は負荷の小さい時には、高速度電動機の場合の方が低速度電動機の場合より、逆に非常に大きくなる。
しかしながら、このような負荷の小さい使いかたは少いので能率の減少はあまり重要でない。
4.55 図は 125HPの高速度電動機と低速度電動機の効率の比較を示す。
A曲線は定格速度 2,440rpm、最大速度 4,500rpmの電動機の場合を示しB曲線は定格速度 800rpm、最大速度 1,800rpmの電動機の場合を示す。
高速度電動機と低速度電動機とでは負荷に対する効率曲線の傾向が全く違った変化を示していることが
4.55図からうかがえる。 |
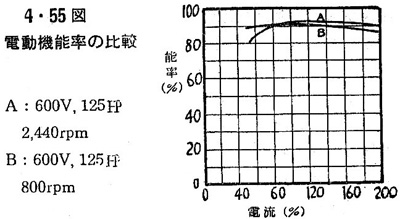 |
4.12 補償電動機 top
弱界磁率を極端に小さく(25〜20%程度まで)して、SRPをさらに大幅に増大させるために、補償巻線を附加することが考えられる。
これは補償巻線を設けることによって電機子反作用を積極的に大きく減少させるもので、一般に n個の補償巻線溝を極片に設ければ、理想的には電機子反作用は非補償の場合の 1/n から 1/(n+1)となる。
4.56図は非補償の場合で、4.57 図は補償巻線溝 n=2 の場合を示す。
通常の電車電動機で設け得る補償巻線溝数は 4〜6個であるから、電機子反作用は 1/4〜l/7となり、界磁歪率を非補償の場合と同一にするとして界磁アンペア・ターンは理論的に1/4〜1/7 となる。
あるいは電機子アンペア・ターンを増加フしてもよい。
このときは主極磁束を減少せしめることができる。
そのほか電機子径・整流子径をより小さく設計し、また回転数も高くとることができる。
しかしこれらのことは主極空隙長が機械的にある限度以上には小さくできないために、界磁アンペア・ターンはそんなに小さくならない。
また整流子片ビッチも限度以下にはできないから、これらのことは全部完全に実現することは困難である。
従って補償電車電動機は本質的に安定度は高く、電動機スペースが小さく、スピード・レショを高くとるためによく行われる極端な弱界磁運転に際してはその優位性を発揮する。
従ってドイツの最近の文献(注16)には補償電車電動機は高く評価されており、またわが国でもスピード・レショの広く要求される大形のディーゼル電気機関車用主電動機や、電車でも直流直巻電動機の欠点である高速性能の悪いことを補うために極端な弱界磁制御を行う電動機に実施された例が若干ある。
補償電動機では安定度が極めて高くなるから過渡的悪整流にも耐え得るし、また最近の高速度電動機に要求される電気ブレーキ時の高電圧大電流にも信頼性は大きくなる。
しかし電機子反作用の完全補償は、実際には構造的に不可能なことが多く、また電機子巻線と全く逆で同一の特性をもつ補償巻線を設けることも実際には不可能である。
また極めて工作が困難であり従って経費も増大する。
また地絡の危険性が若干増大し、これに対しては固定子要部の予備品を用意せねばならない。 |
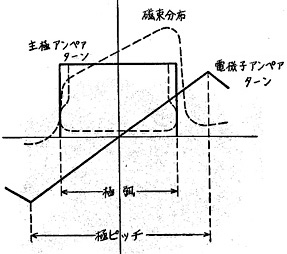
4.56図 非補償電動機
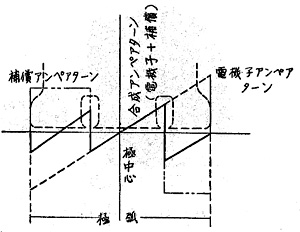
4.57図 補償電動機
|
すでに述べた如く、最近の低端子電圧で電機子に重巻を採用した高速度電動機の設計技術にしたがえば、あえて補償巻線を設けなくても整流子片間電圧は元来低く、また電機子アンペア・ターンも最初から小さい。
従って若干鉄機械(磁束機械)の傾向となり相当な弱め界磁でも決して安定度を失わないような界磁の設計が可能であり、実際の設計に当ってはこのことが留意されている。
さらに注意すべきことは補償巻線付の場合は励磁特性の非直線性が大きくて飽和特性が顕著なために(これは主極空隙に消費するアンペア・ターンを通常の電動機の場合は大きくとっているのに反して小さくとっていることによって起る)、例えば補償巻線付の場合で25%まで弱界磁運転が可能であっても、その時の主極磁束量は通常のものの 35%程度の弱界磁相当の磁束量と変化がないこともあって、これが電動機高速性能が結果として悪くなることであって弱界磁で補うことになる。
またすぐれた設計の非補償高速電動機があって、それを補償巻線付に設計変更を試みても若干の安定度の増加を除いては、電動機の高速化、重量の軽減は殆んど不可能であることが経験的にいえるし、また文献などに見られる電動機が決して卓越した高速軽量でないことを見ても、補償巻線付電動機はまだまだ多くの問題を含んでいるものといえる。
top
***************************************
|