**************************************
INDEX 1
2 3
4 5 6
7 8
9
5章 駆動装置
5.1 駆動装置の諸方式 top
分離駆動方式の研究の動機は電車騒音の軽減を目的として出発し、電車騒音の主たる音源である
@ 軌道に与えるバネ下重量の衝撃に原因する騒音
A 歯車の噛合に原因する騒音
を除去するため
a バネ下重量の軽減
b 無騒音歯車装置
の研究が始められた。
これらの研究の最初の試みは、自動車と同じような駆動方式を電車に導入してベベルギヤーとカルダン軸を使用したものであったが、以来各種の駆動方式が生み出され新製される電車は例外なく、分離駆動方式を採用しバネ吊りされた高速度電動機から車輪への可撓動力伝達の方式についての研究と進歩はここ30年来、まことに多種多彩であることは、3章において概要記述した通りである。
現在、日本における電車の分離駆動方式は台車装荷用の駆動方式で
@ 直角力ルダン方式
A WNドライブ方式
B 中空軸電動機式平行ガルダン方式
が広く採用されている代表的駆動方式であって、いずれも電動機は台車に固定され、電動機軸より可撓継手を経て小歯車軸に動力を伝達する。
5.1.1 直角ガルダン方式 top
5.1図は直角カルダンドライブの略図を示す。
推進軸は十字軸自在継手およびスプライン軸部からなり、電動機と車軸間に相対変位があっても円滑にトルクを伝え得るようになっている。
十字軸は従来自動車の推進軸に用いられている十字形の軸受部と、これに嵌合する2個のフォーク形の自在継手を2組用いたもので、軸バネの伸縮に伴なう上下方向の相対運動を許しつつ動力を伝達する。
歯車装置は直角方向に動力を伝達する必要があるのでベベルギヤーが使用される。
特に歯車噛合音の防止の見地からスバイラルベベルギヤーなど特殊な歯車が使用されるが、最近の直角カルダンドライブの大きな特長は、PCC電車の如くハイポイドギヤーを採用している点てある。
ハイポイドギヤーは大歯車比が許し得るし、ピニオンの機械的強度も大きいという特長がある。(5.2図、5.3図、5.4図)
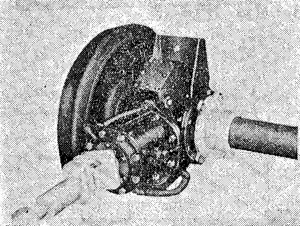
5.3図 直角カルダン駆動装置
|
|
5.1図 直角カルダンドライブ
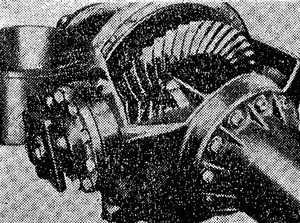
5.2図 ハイポイドギヤー装置
|
(1)ハイポイドギヤー
@ハイポイドギヤーの発展と経過
ハイポイドギヤーはハイバボロイドギヤーの一種である。
すなわち軸が平行なスパーギヤーではピッチ面が円筒、軸が交わるベベルギヤーではビッチ面が円錐であるのに対して、軸が喰違っている場合には、それが回転双曲面(Hyperboloid)となる。
Gleason社では1925年に、これまでスパイラルベベルギヤーの両切用の歯切盤を用いて理論的には線接触するハイパボロイドギヤーを発表し、その後ほどなくパッカード自動車に採用されてこのような線接触するハイパボロイドギヤーをハイポイドギヤーと名付けたのである。
それよりハイポイドギヤーという言葉は主としてグリーソン社の方法で歯切りし、線接触するハイパボロイドギヤーに対してのみ用いられるようになった。 |
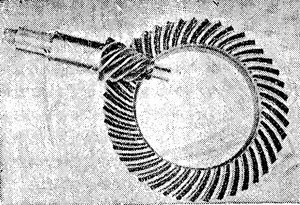
5.4図 ハイポイドギヤー・ピニオン
|
この歯車にはいろいろな長所があるので次第に多く採用され、それまで自動車の後車軸駆動に用いられていたベベルギヤーは次第にこれに置換えられて最近のアメリカの自動車には殆んど全面的にハイポイドギヤーが採用されており、ヨーロッパの自動車でもかなり多く使用されるようになった。
日本でもGleason歯切機械がぼつぼつ設備され主として自動車用にこの国産ハイポイドギヤーが採用されているが、電車用としては、未だ需要も少く、アメリカのGleason社からの輸入による歯車を装備している現状である。
線接触のハイパボロイドギヤーと比較して点接触するハイポイドギヤーは理諭上劣っているように考えられ、完全に正しい歯形のパイパボロイドギヤーが正しい位置で線接触して噛合えば、荷重はその線上に分配されるから理想的の如く考えられる。
しかし実際には歯切誤差のため線接触する筈の歯車が片当りするおそれがある。
また、かりに歯形が完全に正しくともギヤーケースへの取付誤差があれば片当りが起る。
一般に焼入歪は捩れ角が小さくなるような方向へ起り、その量は大小両歯車で異り、ピニオ=ンの方か大きいから、理論的に線接触するように歯切りした歯車を焼入れすれば当然片当りする。
また、無負荷の大きに線接触していても、負荷すれば値が変る。理論上線接触する歯車は,、理想的であっても、低速でしかも軽荷重でない限り実際にはその効果を期待することはできない。
Gleason社がハイポイドギヤーの製作に当って苦心したのはこの点であった。
すなわち荷重による変形と、材料の焼入れ歪に対して歯切の際歯面の適当な箇所に当り位置を選び、荷重が加ったときの歯面の弾性的変形によって適度の当り面積を得るようにした。
A ハイポイドギヤーの長所
ハイポイドギヤーが自動車をはじめ、PCC電車などに盛んに採用されるようになったのは、これが従来用いられていたスパイラルベベルギヤーに比して多くの長所をもつからである。次にこれらの長所について説明する。(5.5図)
(a) ベベルギヤーによるよりも歯車比が大きくとれる。すなわち、ギヤーのある捩れ角に対して一定のピニオン径で捩れ角を増加すれば、円周ピッチは大となり歯数が誠少し、従って歯車比は大となる。
(b) ハイポイドギヤーの設計上重要な値に拡大係数があるがこれは同じ大きさのギヤーに対するハイポイドギヤーとベベルギヤーの大きさの割合であって、普通1.3〜1.5にとる。
つまりハイポイドギヤーはベベルギヤーよりもピニオンが大きいことを意味し、従って大きい荷重が伝達できる。
これはハイポイドギヤーの捩れ角の差異による。
すなわち、ギヤーの歯の捩れの方向にピニオンをオフセットすれば、ピニオンの捩れ角はギヤーよりも大きくなる。
しかるに歯直角ピッチはギヤー・ピニオンとも等しいから円周ピッチは捩れ角の余弦に反比例して、捩れ角が大きくなるほど大となる。(5.6図)
(c) ベベルギヤーよりも噛合率が大きい、ハイボイドギヤーでは捩れ角が大きいので、ヘリカルギヤーと同様に噛合率が増加し、従って荷重は多くの歯に分配されて噛合が円滑に行われ、振動や騒音が少ない。 |
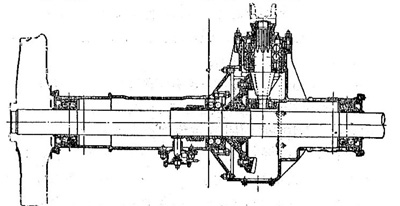
5.5図 PCCカー用歯車装置
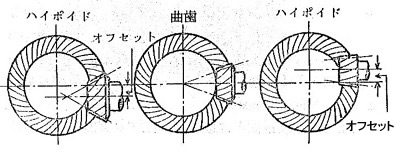
5.6図 ハイポイドギヤーのオフセット
|
(d) ピニオン、およびギヤーの剛性が大きい。これは軸が喰違っているために、ギヤーおよびピニオン軸のそれぞれの両端に軸受を設けることができるからである。
(e) ベベルギヤーよりも寿命が長い。例えばトラックでは、普通ピニオンのオフセットをギヤーのピッチ円直径の約1/10に制限するが、寿命が4〜10倍伸びたことから明らかなようにハイボイドギヤーでは大きなオフセットをとるから寿命は著しく長いことがわかる。
(f) ハイポイドギヤーではオフセット量だけ推進軸が低くなり、台車重心もそれだけ低くできて安定度がよくなる。
普通オフセット量の最大はギヤー径の約30%である。
(g)ハイボイドギヤーの製作費はとくに増加しない。
これは歯切に特別な歯切盤を使用する必要はなく、Gleason式歯切盤で歯切ができるからである。
ハイポイドギヤーはスパイラルベベルギヤーと較べてピニオンの曲り角度が大きく、ギヤーの曲り角度は小さい。
スパイラルベベルギヤーは5.7図に示す通り歯の両側の圧力角と歯形曲線は全く対称で等しいが、ハイポイドピニオンは5.8図の如く非対称の歯形曲線となり、両側の圧力角も異なる。
(h)効率は低くない。自動車用のハイポイドギヤーの捩れ角は普通30〜50度であるが捩れ角が45度のウォームギヤーに比較して歯面の滑り速度は1/3以下である。
(i)ハイポイドギヤーのすべての歯は転りのみならず、滑りをもって噛合う。
従って歯面上の滑り速度の分布状態はベベルギヤーよりも遙かに均一であるから、ラッピングの際歯形を損うことがない。
B ハイボイドギヤーの潤滑油
ハイボイドギヤーを使用するときの重大な問題はいわゆる極圧潤滑油(Extreme Pressure Lubricant)を使用せねばならぬことである。
高荷重のもとに滑り運動が働いているハイボイドギヤーにおいては圧力が高くなると荒い面の凸部が局部的に高温となり、石油系潤滑油の局部的排除・化学的分解・金属間の接触および焼付などが生ずる。
これを防ぐために極圧添加剤(極温添加剤)を鉱物油に添加した潤滑剤を使用すると、高い局部温度のもとで面の突起部と化学化合物を形成し、これらの化合物は薄い膜となって金属面に滑らかな面を形成して金属相互の摩擦より少い摩擦を生じ、また極度の局部圧力を軽減し温度を低下させる。
極圧(EP)潤滑油とは接触部に生ずる実際の面圧力に耐えて面の溶着や摩耗を防止する潤滑油のことであって、極圧添加剤としては緩性ナンテン酸鉛がAGMA規格に示されている。
(2)直角カルダン方式の優劣
面角カルダン方式を他の駆動方式と比較すると概ね5・1表の点が指摘される。 |
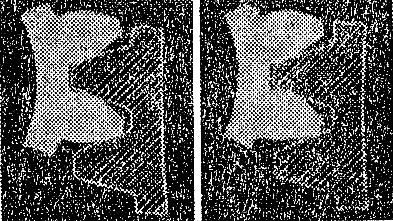
5.7図 スパイラルベベルギヤーの噛合(左図)
5.8図 ハイポイドギヤーの噛合(右図)
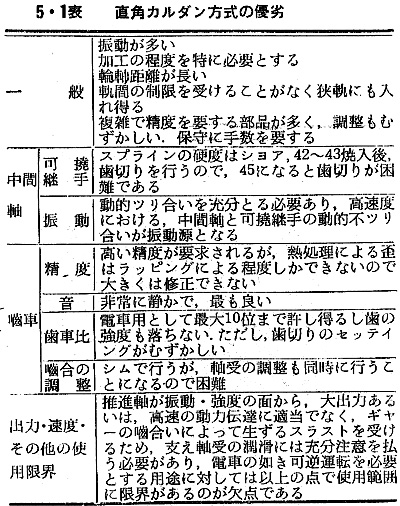
|
5.1.2 WNドライブ方式 top
WNドライブの名称は Westinghouse社のWと駆動装置を製作した Nuttal 歯車会社――現在 Nuttal はWH社に合併され、同社の歯車製作工場となっている――のNとをとって命名した駆動方式である。
5.9図はWNドライブ方式の略図を示す。
電動機は車軸に平行に台車枠に固定されており、減速歯車装置は頑丈な一体鋳鋼または鋼板溶接製で車軸にテーバーコロ軸受を介して強固に収付けられたギヤーケースに内臓されている。歯車装置は、へリカルギヤーで、ピ二オン軸は、いわゆるシャフト・ピニオンであって、軸に歯切りをした形のものであるから、従来の釣掛式の場合のピニオンとは趣を異にしている。 ビニオン軸もギヤーケースにテーバーコロ軸受を介して取付けられている両持ち軸受であるので、ビニオンとギヤーとの歯車中心距離は正確に保たれている。
従ってギヤーとの噛合いは極めて円滑で運転は静粛である。
歯のモジュールも従来の釣掛式に較べると1/2〜2/3程度にまで小さくすることが可能であるため1段減速で 8:1 程度の歯車比も許し得ることとなった。
ギヤーケースはピニオン軸側で長い吊ボルトによってゴムを介して台車横梁に支持されているので電動機軸とピニオン軸との変位を最小にして、カップリングの無理を減少させている。
ギヤーケースには車軸の軸受電蝕防止用として接地装置が附属している。
歯車装置およびコロ軸受の潤滑はギヤーケース内の潤滑油で行い、コロ軸受は歯車の回転によってかき上げられだ潤滑油が各軸受に流れ込みコロ軸を潤滑してギヤーケースの底部におちる構造となっている。
一体構造のギヤーケースは完全なオイル・タイトであるとともに軸受の歪を防止する点て割型に勝っている。
5.10図に駆動装置の概要を示す。 |
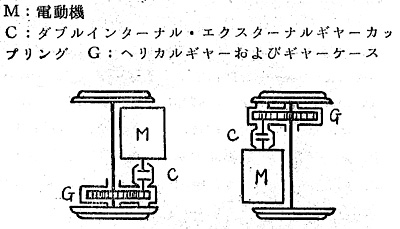
5.9図 WNドライブ
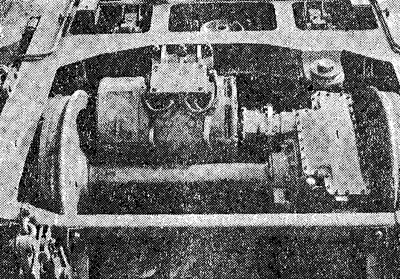
5.10図 WNドライブの電動機および駆動装置
|
(1)ギヤーカップリング
WNドライブの特長は電動機軸とピニオン軸との間を結ぶ可撓継手としてギヤーカップリングを使用している点にある。
これは極度に歯をクラウニングした2組のインターナル・エクスターナルギヤーを組合せたもので、5.11図に示す如く軸の偏心または傾き対しては自由に可撓伝達が行える。
この継手は普通の十字継手または撓みみ板継手などと異なり、多数の歯により連続的に動力伝達が円滑に無理なく行えるのが特長である。カップリングの歯の潤滑はスリーブ内のギヤーコンパウンドによって行う。
WNドライブは、ギヤーカッブリングの軸方向の寸法が長いために狭軌の台車に収容することは困難と考えられていたが、最近では軸方向の長さの短い狭軌用のものが三菱電機で開発され、その使用範囲が拡大された。
下の(5.12図、5.13図)
(2)WNドライブ方式の優劣
WNドライダブ方式を他の駆動方式と比較すると概ね右下の5.2表の点が指摘される。
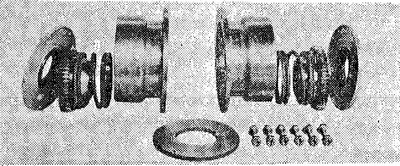
5.12図 WNギヤーカップリングの部品(上)
|
|
5.11図 WNギアカップリング作用
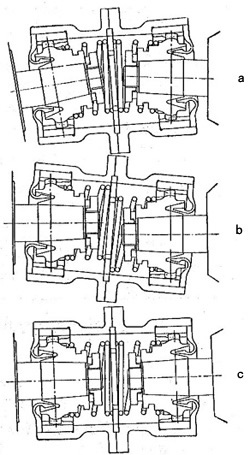 |
5.13図 WNギヤー・ピニオン(下)
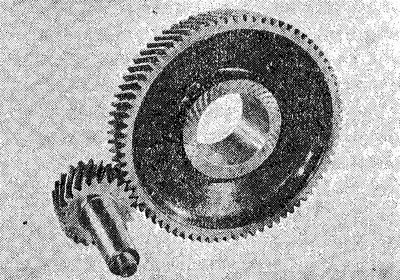 |
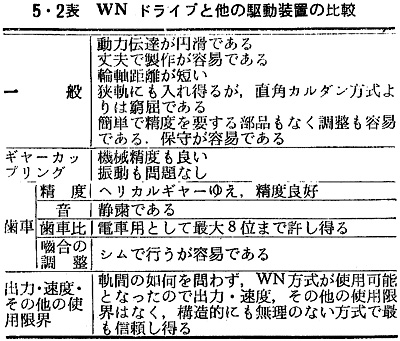 |
5.1.3 中空軸電動機式平行カルダンドライブ top
5.14図は平行カダンドライブの略図を示す。
電動機は車軸と平行に台車横梁に固定され、電機子軸は中空で電動機軸端はギヤーケースと反対側にある。
歯車装置は車軸に圧入されたヘリカルギヤー、これと噛合うピニオンおよび割型のギヤーケースからなり、ギヤーケースとピニオン軸は円錐コロ軸受で支えられている。
ギヤーケースはピニオン側上方を台車枠より、ゴムを介してリンクにより垂直に吊られてトルク反力を支えている。
電動機軸とピニオン軸は電動機の中空軸を貫通する動力伝達用の撓み軸、およびこの両端の可撓継手から或るカルダン軸によって連結されている。 |
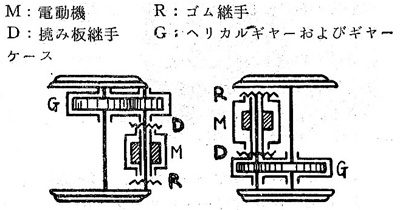
5.14図 中空軸平行カルダンドライブ
|
この電動機の中空軸と動力伝達用の捩り撓み軸との間の遊隙は、バネ上の電動機゙とトルク反力による緩衝ゴムの撓みや台車軸バネの撓みにより相対的に動くピニオン軸との間の変位に対し充分余裕のあるよう設計する必要がある。
ギヤーケースには車軸の軸受電蝕防止用として接地装置が附属していることは、直角カルダン・WN方式などと同様である。
歯車と軸受は共通の潤滑油により潤滑される。
軸受の潤滑は歯車の同社による油の飛沫がギヤーケース上部カバーの樋に溜って、各軸受に流れ込み、余分の油はギヤーケース底部に滴下する方式である。
5.15図の構造説明図の如くこの方式はBBCディスク・ドライブと類似の方式であって、この方式の特長は電動機の中空軸内を貫通する可撓伝動軸(動力伝達用捩り撓み軸)と可撓継手にある。 |
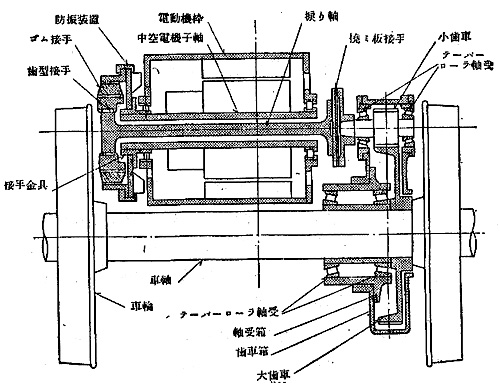
5.15図 中空軸平行カルダンドライブ断面
|
(1) 可撓伝動軸と可撓継手
可撓伝動軸はゴム継手などの緩衝談置とともに、その捩り撓み作用によってレール面からの衝撃回転力の緩衝作用を行うほか可撓継手とともに可撓伝動作用を兼ね行っている。
電動機軸端側の可撓継手としては薄鋼板を短冊形としたもの、または弾性ゴムとインターナル・エキスターナルギヤーよる歯形継手とを併用したものなどがある。
ピニオン側撓み板継手は薄鋼板を数枚重ねしたものである。
電動機軸端側を撓み板継手によるか、歯形継手によるかは軌条の良否・速度・負荷および軌間などによって決定されるが、撓み板継手は軸方向が短く摩耗部分がないため保守が簡単であるが、一方偏角の大きい所には使用できない。(5.16図、5.17図、5.18図)
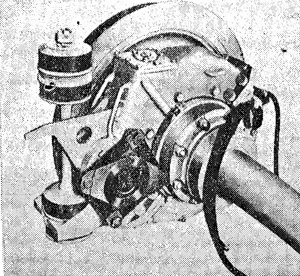
5.17図 中空軸平行カルダンギヤーユニット
|
|
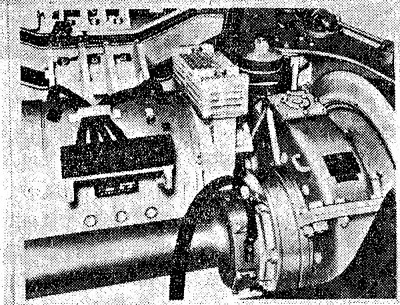
5.16図 中空軸平行カルダン駆動の電動機と駆動装置
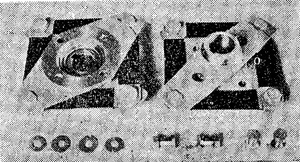
5.18図 撓み板継手部品
|
(2) 中空軸電動機式平行カルダンドライブの優劣
@ 伝動軸の捩りバネ作用を利用してレール面からの動力伝達系に伝えられる衝撃を緩和している。
A 伝動軸が電動機軸を貫通している関係上これを長くすることができ、従って電動機とビニオンの相対変位に応ずる撓み板継手の偏角が少いので強庭上有利である。
B 自在継手として薄鋼板製の撓み板継手を使用しているので摩耗部分がなく構造が簡単であるほか、軸方向の寸法が短縮されるので、重量が軽減される。
C 歯車は、ヘリカルギヤを使用しているので騒音が少い。
D 伝動軸が電動機中空軸内部を貫通しているので、中空軸と伝動軸との間に充分の遊隙を必要とする。
E 中空輸の電動機軸のため、電動機の転り軸受の内径は必然的に増大するため前述のdn値が増大し、軸受の限界速度の制限を受ける。
5.2 釣掛式と台車装荷式との電動機の受ける振動衝撃の比較
top
釣掛式電動機がどの程度の衝撃を受けているかについて住友金属製鋼所が京阪神急行京都線において実測した結果によると、時速120kmの時、整流子点検蓋の上で、26〜27hz 20g、車軸受で 20〜30g、台車中央で 1g程度の振動の加速度である。
従って、バネ吊りされた電動機の受ける衝撃加速度は1g程度と推測される釣掛式が最大 20〜30gであるのと比較すると非常に小さいので電動機の強度上または閃絡防止上などから見てはなはだ有利である。
さらに近鉄と三菱電機との共同で近鉄奈良線八戸里−西大寺間で現車振動試験を行った結果によると、台車装架WN駆動電動機は釣掛式電動機に比べて遙かに振動衝撃から解放されているこどが立証された。
その結果の概要の一端を紹介する。
@ 試験実施年月 1955年10月
A 編成(5.19図)
B 試験区間 八戸里−西大寺各2往復
C 振動計取付位置 電動機磁気枠(整流子点検窓横)・ブラシ支え
D 振動計
電子管加速度計は雅子管の陽極板にとりつけられたアルミ棒の加速度による振れが、電子管に流れる電流を変化させることを利用したもので、この変化を増巾して電圧の変化として記録するようになっている。
E 台車
600形 日車製(1948年)
800形 近車製 KD-12(1954年) |
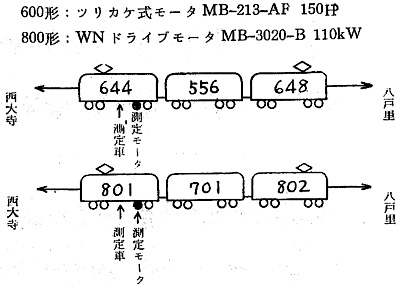
5.19図 試験電車の編成
|
F 振動記録の一例(5.20図)
G 振動周波数
走行時の各測定点の全走行区間を通じての振動周波数は5.3表の通りで、釣掛式モータのヨークは非常に高周波である。
H 振動加速度
走行時の各測定点の平担線・ポイント・トンネル内(道床岩板)・勾配および勾配における空気制動時における振動振幅から振動加速度を求めたもののうち2〜3を下の5.21〜5.24図に示す。
振動加速度で走行中最大値を示したのは、釣掛式モータのヨークで勾配変化の箇所で60km/hの速度で空気ブレーキをかけた時であって、その値は実に34gの値を記録した。
一般的には、台車装架式は釣掛式の
約1/10以下であると考えて差支えなかろう。
|
5.20図 電動機振動加速度記録の一例
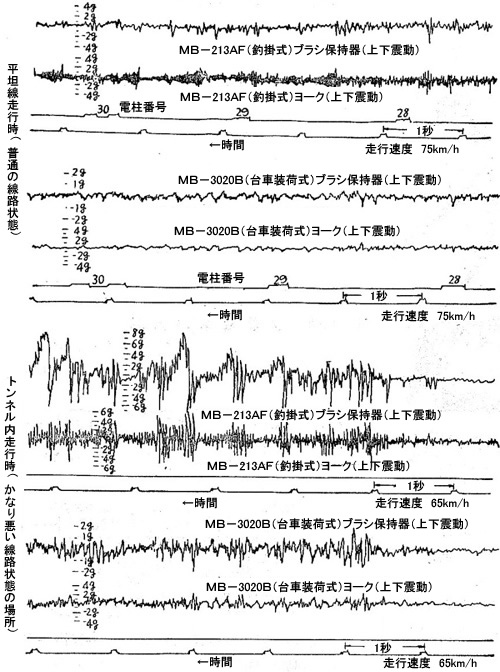 |
5.21図 ポイント通過時のブラシ支え振動加速度(左)
5.22図 勾配でのブレーキ時のブラシ支え振動加速度(右)
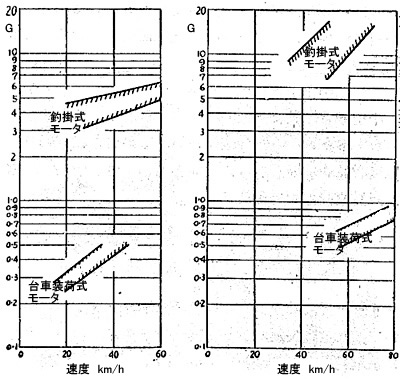 |
5.21図 ポイント通過時のヨーク振動加速度(左)
5.22図 勾配でのブレーキ時のヨーク振動加速度(右)
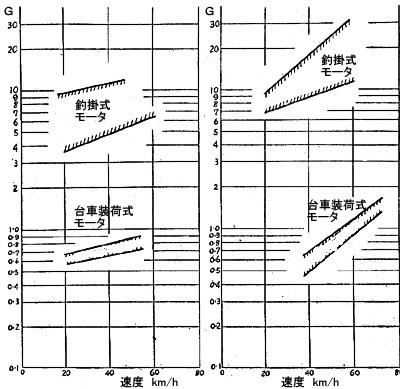 |
5.3 バネ下重量 top
5.3.1 釣掛式電動機のバネ下重量
釣掛式電動機ではその重量の約1/2がバネ下重量となるといわれているが、これの正確な計算例を示すと次の如くである。
衝撃に参加する電動機の動的バネ下重量(電動機重量のみに対する)は次の式で表わされる。
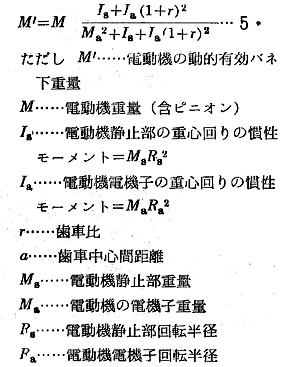
三菱電機製 750V、150HP、釣掛式電動機につき動的バネ下重量M'の計算例は次の通りである。
電動機総重量 1,880kg
車軸受箱(メタルを合む) 104 kg
ギヤーおよびギヤーケース 198 kg
電動機重量(含ピニオン) M 1,578kg
この値に車軸受箱・ギヤー、およびギヤーケースの重量を合めた重量――745+104+198=1,047kg――が電動機の動的有効バネ下重量となる。
これは電動機本体の67%に相当し電動機総重量の55.7%である。
もし歯車に可撓性を与え、バネが充分軟くて衝撃が歯を通じて電機子に伝わらないとすれば Ia=0であるから次の如くなる。
M"=1.578×765/(1,780+765)=475kg
5.3.2 各種駆動方式におけるバネ下重量の比較 top
各駆動方式の日本における実績についてバネ下重量を比較すると5.4表となる。
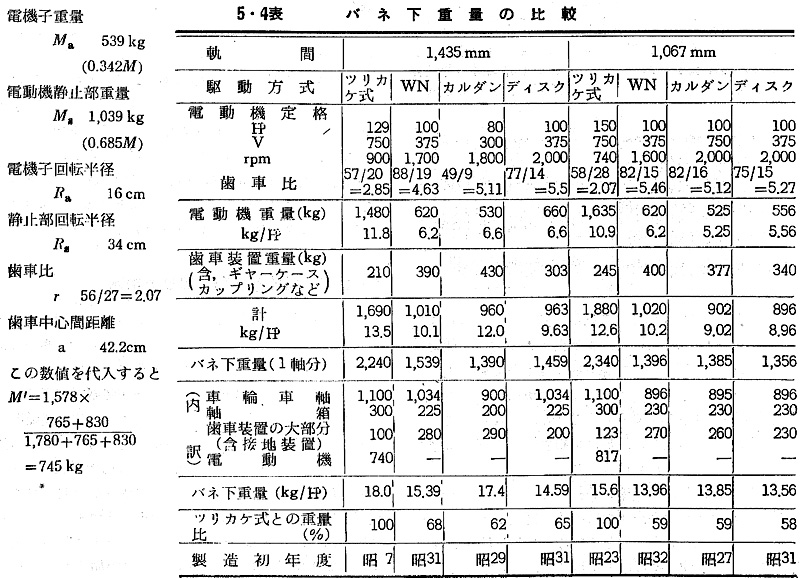
5.4歯車の潤滑 top
5.4.1 潤滑の基礎
いかなる歯車装置においても潤滑は常に必要であるが、スパーギヤーの場合は滑りと転りの組合せの運動からなり、両歯の接触線に向って直角に油をつれ込む作用をなすので、油膜の構成には好ましい状態にある。
この場合は油は隙間の広い部分から、せまい部分に強制的につれ込まれる結果として油圧を生じ、この油膜圧力が荷重を支えるのである。
一般にスパーおよびヘリカルギヤーでは、油膜の構成維持が比較的容易なので、特に高荷重とか振動荷重のかかるものでなければ、必ずしも強粘着力または高粘度の油を必要としない。
ただ歯車の接触の機構から油膜強度の大なる潤滑剤であることが望ましい。
これに対して、おもに相対滑り運動をしているウォームギヤーやハイポイドギヤーなどは常に境界潤滑すなわち非流体潤滑を行う接触の機構にあるので、粘度とともに、その粘着力に重点を置き、しかも油膜強度の大きい潤滑剤であることが必要である。
一般の潤滑と同様に歯車にも流体潤滑と境界潤滑の2種の潤滑が考えられる。(5.25図、5.26図)
完全な粘性油膜でへだてられている潤滑状態がいわゆる流体潤滑で油層が相当厚いために、摩擦面上の突起点が油膜中に完全に沈む。
従って部分的には滑り運動が生じていても、運転状態におこるすべての摩擦は、油層間の油の粘性摩擦で熱を発生するのみである。
これらの熱の一部は潤滑油に持ち去られ、他は金属表面から逐次機械本体に伝達され大気中に放散される。
潤滑油の粘度が高いと厚い油膜ができるので、接触面の間から排出または押出すための油の抵抗が大きくなって、それだけ伝達能力は大きくなる。
しかし粘度が高くなるにつれて、油の摩擦損失を増すのみならず、それは然になって余屈を過熱させて流体潤滑をおびやかし、一方潤滑剤の劣化を促進させるのでやはり適当な粘度のものを選ばなければならない。 |
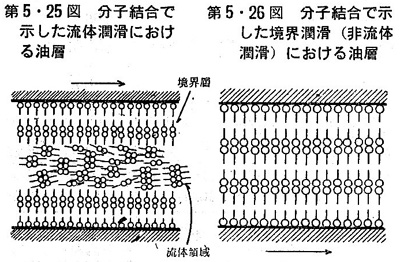 |
もちろん潤滑油は液体であるから、ある程度の圧力が相当時間作用すると、どんな粘度の油でも境界潤滑すなわぢ非流体潤滑がはじまって、相対する歯面に仰しつけられる。
このような状態は常に摩耗を伴うため避ける必要がある。
流体潤滑では如伺なる場合にも摩耗は存在しない。
接触面の間からの潤滑油の排出を最小にする手段としては、圧力を低くするか、作用する時間を短かくするかの2方法がある。
従って低圧力、高い滑り速度に対しては粘度の低い油を用い、高荷重・低速度では粘度の高いものを用いることが望ましい。
5.4.2 油の粘度 top
温度が高くなるにつれて潤滑油の粘度は低下するが、その低下する割合の小さいものを粘度指数が高いといい、大きいものを低い指数という。
歯車の運転温度がかなりの範囲にわたるときは、粘度指数はSAE−60以上、普通の状態では20以上とされている。
ウォームギヤーやハイボイドギヤーのように、滑り運動を多く伴う歯車は永久的な境界潤滑を呈していて、ことに低速では著しいが速度の上昇とともに流体潤滑となるので状態は良くなる。
このような場合に温度上昇とともに粘度が低下することは有利である。
粘度の高い油ほど良い境界潤滑油となるので、起動の際、または低速状態ではより好ましく、高速状態に達すると押出しの時間が短かくなるので、高い粘度は必要としない。
粘度の低い潤滑油が歯に附着していると、早く熱を発散して、粘着力が小さくなるので歯車効率が上昇する。
すなわち温度上昇とともに歯車効率は上昇する。
5.4.3 極圧添加剤(EP添加剤) top
一般に仕上面が滑らかであればあるほど、歯の突起部の接触し合うことがほとんどあり得ないので、摩耗は減少し、たとえ油膜が薄くとも流体潤滑を脱することがなくなる。
従って馴染んでいる機械装置が実用的であるという根本的な理由がここから考えられる。
実際問題としては、理想的な滑らかな面を仕上げることは不可能であるし、たとえ理想的に滑らかな面が得られたとしても、種々の理由によって、ほとんど滑らかな面のままの状態に留まることがない。
そこで止むを得ずして生ずる境界潤滑を、できるだけ害のないようにする別の方法として、極圧潤滑油あるいは極圧添加剤の如きものに頼らねばならない。
これは高荷重のもとに滑り運動が働いているハイポイドギヤーに対して特にあてはまる。
極圧添加剤(Extreme Pressure Lubricant)の研究は1925年、アメリカの Gleason社がはじめてハイポイドギヤーの歯切に成功し、翌年パッカード自動車に採用したのがはじまりであって、ハイポイドギヤーは特殊な設計であるために、きわめて高荷重で、しかも摩擦速度が早いことから、普通の潤滑油ではその用をなさなくなってきた。
このような苛酷な摩擦面の潤滑に、なおよく潤滑作用をいとなむ潤滑油の必要に迫られ、その対策として極圧添加剤の研究を始めた。
極圧添加剤の作用は、金属の表面に圧力にも、熱にも強籾な薄膜をつくり、これが高圧・高温下において有効に働き、摩擦面金属の直接の接触を防止して溶着や摩耗を防ぐものである。
この種の添加剤としては、脂肪酸の鉛石鹸・硫黄・燐または塩素化合物などがよく用いられている。
5.27図は極圧添加剤の作用を示す。
図において黒色部は、面の突起部における局部高温によって作られた添加剤と、金属面との開の化学化合物を示すが、この化合物は滑らかな面を形成させるために、次第にすりへってゆく。
すなわち極圧添加剤は、極圧にともなう摩擦面の極めて高い温度が、その効果をもたらす主因となるのであって、油膜が薄くなって、そのために摩擦が急激に増大して、局部的に一種の焼付きがはじまるようになると、はじめてその箇所の高圧と高温のために添加剤の分解と、新しい反応とが起り、そこに特殊な金属皮膜が生じて、金側相互の摩擦より少い摩擦を生じ、また極度な局部圧力を軽減し、温度を低下させる作用をする。 |
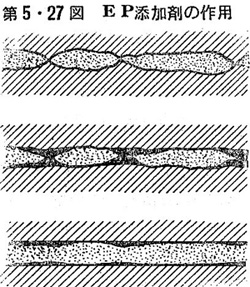 |
top
***************************************
|