**************************************
12 走り装置(田中隆三の電気機関車読本 Y)
T
U
V
W
X
Y
Z
[
\ |
まえがき
1 電気機関車の生いたち
2 電気機関車の種類
3 電気機関車の特性
4 電気機関車の呼び方
5 電気機関車の機器配置
6 主回路の機械・器具
7 高圧補助回路の機械器具
8 高圧付属回路の器具
9 制御回路装置の機器
10 電灯装置
11 台車
12 走り装置
13 ブレーキ装置
14 電気機関車の制御作用
15 電気機関車の運転 |
12.1 歯車装置
12.1.1 小歯車
12.1.2 大歯車
12.1.3 歯数比
12.1.4 歯車箱
12.2 車輪
12.2.1 タイヤ
12.2.2 車軸
12.3 軸箱 |
12 走り装置
車両の走行部分を總精して走り装置というが、電気機関車では、主電動機の大歯車から車輪までの間の部分を走り装置と称し、歯車装置・歯車箱・車輪・軸箱などを指していう。
12.1 歯車装置
top
電気機関車には各種の歯車があるが、主電動機の回転を車輪に伝える歯車とこれに関連をもった装置をとくに歯車装置といって、他と区別する。
歯車装置は電動機軸に取付けた小歯車、これにかみ合う大歯車とこれらを納める歯車箱をいう。
12.1.1小歯車
top
小歯車はピニオンと称するもので、主電動機の電機子軸端に1/10の細り(テーパ)を付してはめられ、キー及びナットでもって締めつけられる。大歯車とかみ合う様子は第81図に示す通りである。
普通15〜30枚位の歯数を有し、主電動機の回転力を大歯車に伝えるととも大歯車1回転に対し、3〜5倍くらい回転するので、特に歯を丈夫にするためにニッケル・クロ−ム鋼で作る。
12.1.2 大歯車
top
大歯車はギヤと称するもので、動輪軸に水圧をもって圧入され、キーで固定される。 |
第81図 歯車装置
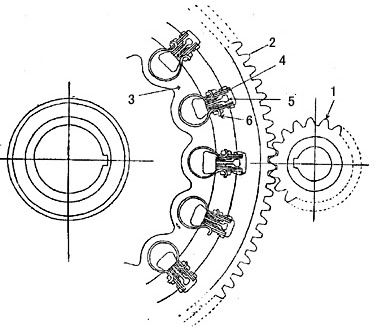
1 小歯車、2 大歯車(歯車輪)、3
大歯車(歯車心)、
4 板バネ、5 挟み板、6 止金
|
大歯車は普通70〜90枚の歯数を有L、特殊鍛鋼で作られた歯車輪(2)と鋳鋼製の歯車箱(3)とで出来上っていて、歯車輪は歯車の周囲に軽くはめられるが、これらの間には16組の板バネ(4)が止金(6)を挾んで挿入されているから、歯先に受けた回転力は一旦板バネの撓みでその衝撃を吸収して、撓みが一定の値になるとき、はじめて歯車軸に伝えるしくみになっている。
従来は小歯車はもちろん、大歯車においてもバネを使用しないものがあったが、近時電気機関車は、漸次強力・高速度のものが製作されるに及び、歯車輪と心とが一体となったものでは衝撃のため歯先が折損したりかみ合い時の騒音はげしく且つ磨耗も多いので、最近において再びバネ入大歯車を使用するようになった。
またバネ入小歯車についても研究が進められている。
板バネは初圧が高くてその作用が確実でないので、最近は蔓巻バネを6組円周方向に挿入したものが用いられる。
このバネはバネ棒の直径22mm、バネの平均直径80mmや、6巻のものを用いる。
歯形はインボリュート曲線(注1)をもったもので、磨耗を少くするために歯形に長短アデンダム補正が施されている。
(注1) インボリュート歯形とは円の周に巻きつけた糸を引張りながらほぐして行くとき、糸の1点が描く曲線をいうので、ちようど歯形の半面を形づくる。現在普通に用いられる歯形はほとんどインボリュート歯といってよい。
アデンダム補正とは、歯車の刻み円から歯先までの歯末(アデンダム)を、小歯車は長く大歯車は短くとって、このアデンダムを歯の作用高さの半分より小歯車は長く、大歯車は短くとることをいう。
こうすると、小歯車では刻み円の歯の厚さが大きく、大歯車は小さくなるので、摩耗が平均化され、且つ小歯車の直径を小さくとることができるので、大きい歯数比をとることができるからである。
歯車の各部名称は第82図の通りである。
電気車の歯形はすべてモジュールと称する(注2)。
(注2) モジュールは歯車の性能を表現した呼び方であって、刻み円直径(mm)を歯数で割った数値をいう。
この値の標準は無名数の10及び12があって、電動機出力200kW以上に対しては12を用いるから、電気機関車用歯形のモジュールは全部12といってよい。 |
第82図 歯車各部の名称
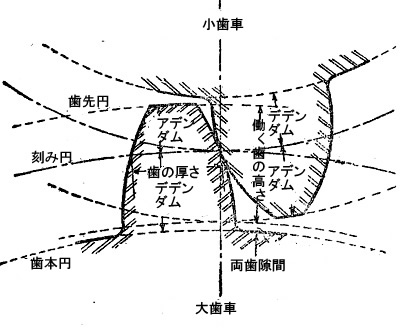
|
12.1.3 歯数比
top
大歯車の総数を小歯車の総数で割ったものを普通歯数比(ギヤレシオ)という。
歯数比の最小値は1であるが、電気機関車の歯数比は普通2〜5である。代表的機関車の歯数比は第3表の通りである。
歯数は直径に比例する。
そして電機子軸と動輪軸との中心距離を変えることはできないから、歯数比を受えて旅客用を貨物用に、または貨物用を |
第3表 代表的電気機関車の歯車比
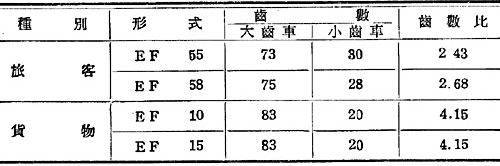
|
旅客用に変える場合、あるいは単に歯数比を変えて性能を変える場合には両歯車の中心距離、すなわち半径の合計、言い換えれば歯数の合計を一定にせねばならない。
上の例において、各形式とも歯数の総計はいずれも103枚であるのはこの故である。
歯数比の大きいことは、大歯車の回転数すなわち動輪の回転数を滅らすことであるから、速度性能の低い機関車になるが、一方において電動機の出力は一定の電流値に対しては不変であるから、牽引力は速度の滅っただけ増加する。言い換えると、速度は総数比に逆比例するが、牽引力は比例して増減する。
よって歯数比の小さい機関車は牽引力は小さいが速度の高い性能を有し旅客用に適するし、またこれと反対に歯数比の大きい機関車は速度は低いが、牽引力の大きい性能を有し貨物用機関車に適する。
第3表によっても旅客用機関車は歯数比は小さく、貨物用機関車は歯数比が大きいことが分る。
12.1.4 歯車箱
top
歯車箱は大・小歯車をまとめて訥めた軟鋼で作ツた一つの共通な箱であウて、第83図に示すような形をしている。
歯車箱は車軸の軸箱に相当するところで、歯車の磨耗を防ぐために給油装置の役目をするとともに、歯車のかみ合せ部に異物の入らないように保護をする。
この目的のために、歯車箱の構造は、
@ 歯車に適した粘度の高い油を保有し且つ高い速度で油をはね上げても漏油しないこと。
A 歯車の状態を時々外部から点検できること。
B 電動機に固定していて振動に耐え充分な強度を有すること
等の条件を備える必要がある。
しかしながら歯車箱は電機子軸と動輪軸の二つを貫通しているために図のように上下に割れる構造となるので、合せ目の設計にはいろいろと工夫される。
軸部の上下には図のように溝を作ってフェルトを挾んだり、右端に示したように上下の箱板はフォ−クエンドになっていて密着を保っている。 |
第83図 歯車箱
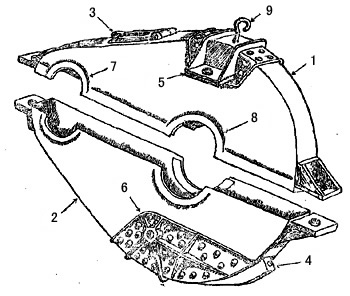
1 歯車箱(上)、2 歯車箱(下)、3 検査蓋、4 油栓、5 上取付金具、6 下取付金具、7 電機子軸穴、8 動輪軸穴、9 鈎 |
検査蓋は上にあるが、別に下部に油栓をもうけて、油量の点検に便ずるとともに注油を行う。
油量は箱底から30mm以上を常に保つようにせねばならない。
歯車箱の合せ目は前後で締め合わされ、これを取付けるには上下2箇所で電動機に支えられる。
12.2 車輪
top
蒸気機関車のように前進・後進がはっきりしている車両と違って、普通一般の電気機関車は何れの方向へも無条件で運転するから,車輪は先輪と動輪の2種類だけで足りる(注3)。
(注3)厳格にいうと、流線形のように前後進の区別あるものでは、名称上は先輪と従輪とに区分できるが、構造は全く同様である。
動輪の構造は一般客貨車の車輪と全く同様で、軸心・タイヤ・車軸の3部分から成る。
軸心は鋳鋼で作られ、ボス・スポーク・リムをもって組立てられる。
タイヤは炭素鋼で作られ、リムの外側はタイヤ止輪をもって固定され、車軸は鍛鋼で作られ、軸心ボスに水圧をもって圧入されることは、他の車輪と変りはないから、ここでは主として電気機関車のとくに変わった点について述べよう。
電気機関車の動軸は一方の車輪に接近して大歯車を水圧で圧入、キーをもって固定することは第86図に示す通りである。
つぎに電気機関車の動輪は専ら電動機を台枠内側の動軸軸につりかける関係上、外側軸受式を用いるので、軸心ポス部の外側は軟鋼板または砲金製のボス当金を当てて軸受側から給油を行い、発熱を防ぐとともにボスの磨耗を防止する。
スポークは蒸気機関車と同様断面惰円形をしているが、それよりも少く13本のものが多い。
これは均一な回転力を受け、且つ直径は小さいからである。 |
第86図 動輪
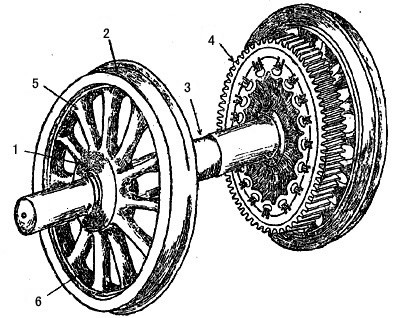
1 輪心、2 タイヤ、3 車軸、4 大歯車、5
スポーク、6 リム
|
タイヤの断面取付方法等は一般車両と同様であるが、前後に台車を有して復心装置の自由が利かないので、事実上固定される軸距離が長いため、フランジの磨耗は一般に多い欠点がある。
このために6軸機関車では中位のフランジを最初から薄く削正して、機関車の曲線通過を容易ならしめているが、なお、第1・3・4・5動輪のフランジ磨耗防止には保守上特殊の手当が必要とされている。
12.2.1 タイヤ
top
タイヤはリムの外周にはめた外輪であって、非常に大きい引張・圧縮力を受けるので抗張力の大きい(75kg/平方cm以上)炭素鋼(STY80)で作られ、軸心リムの外周に焼嵌め(注4)される。
(注4) タイヤを輪心に取付けるには、タイヤの内側径を軸心の外径よりも直径の1/1000だけ小さく削っておいて、タイヤを電気炉等で300度内外に加熱膨脹してはめこみ、タイヤが冷却するときの収縮力で軸心に締めつけさせる。
タイヤはレールを正面から踏みつける踏面と常に内側に車輪を誘導するフランジの2部分から成っていて、踏面には1/l0及び1/20の勾配をつけて直径の内外に差をもうけ、曲線節で左右の車輪がちがった直径で回転することにより、その通過を滑らかにしていることは一般車輪と同様である。
タイヤフランジの磨耗防止について有効とされている方法をあげるとおよそ次の通りである。
@ 中間復心作用を弱めること(中間連結器復心バネの一部撤去を行う)
A 先台車復元力を増加すること(バネ装置調整その他により先台車上の重量を増す)
B レール又はタイヤ水マキを行うこと
C 機関車プレーキの取扱時間をできるだけ軽減すること
D フランジ給油器の適切な利用をはかること
E タイヤの溝つき削りを行うこと
F タイヤの焼入を行うこと
以上のうち、@〜Dは機関区において実施できる事項である。
12.2.2 車軸
top
車軸も動輪軸と先軸とでは構造も太さも著しく違う。
動輪軸は電動機の回転力を片側(大歯車)のみで受けて動輪とともに回転するものであるから、充分な強度を与えることが必要である。
これに対し先輪軸は負担重量は軽くも、直径が小さいために回転数は多くなり、ことに内側軸受式のものにあっては、油受の構造(後述)が小さくなり、発熱の機会を作るので、軸受面を増す必要がある。
電気機関車の動輪軸は外側軸受式であって、特殊のものを除いては鍔はない。
その構造は抗張カの高い鍛鋼材で作られ、第87図のように5段の太さをもっていて、最外側に車軸受(1)を、つぎに輪心部(2)、軸心の内側に電動機支軸受(3)を、また一方の軸心内側電動機支軸受との間に大歯車輪心(4)を嵌入するが、その太さの関係は図示の通りである。
輪軸は歯車軸心部は最も大きい曲げモーメントと剪断力を受けるので、その直径も最大(200mm)であって、且つ太さの変り目にはR=7mmの曲部をもっている。
また、軸心部は輪心に圧入を容易ならしめるため端面に対し細り(テーパ)が付しいている。 |
第87図 車軸
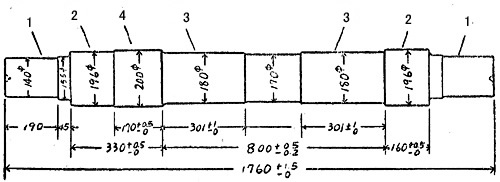
1 車軸受、2 輪心部、3 電動機支軸受、4 大歯車輪心
|
車軸を軸心に嵌入するには車軸輪座の外径を軸心の内径よりも大きくとり(注5)、車軸に白ペイントを塗って水圧で押し込むのであるが、この場合の嵌入圧力は輪心の材質と直径の大きさによって違い、普通動軸で10t、先輪軸では7.5t位である。
(注5) 鋳鋼輪心の場合は車軸輪座の外径を輪心の内径よりも直径の1/1000〜1.5/1000位大きくとる。
先輪軸は、従来内側軸受式のものが専ら用いられたが、油受の容量が小さく焼損多く保守に手数がかかるので、最近の2軸台車は外側軸受式となりつつあるほか、その構造は一般客貨車輪軸と変りはない。
電気機関車動輪の直径は一般に蒸気機関車のものよりも小さく、1250mmを標準としている。
動輪の直径は速度と牽引カとに大きな関係があるが、電気機関車では歯数比によってこの調整はできるから、タイヤ・輪心などの互換性を与えるために標準化したのである。
先輪の直径は960mmを標準としているが、これは一般客貨車・電車と共通である。
12.3 軸箱
top
軸箱は機関車の重量を直接受ける軸受金を内蔵する長方形の箱であって、運転中の衝撃を受ける関係上丈夫な鋳鋼材で作られ、且つ給油装置となるために蓋を密閉して漏油を防いだ構造となっている。
電気機関車の軸箱には動輪用と先輪用とがあるが、動輪用は主として外側式を、先輪用は内・外側両用があることは車軸の項で述べた通りである。
軸箱には平滑軸受(プレンペアリング)用とコロ軸受(ロ−ラベアリング)用とがある。
平滑軸受用とは平滑面を有する受金を介して重量を伝えるものをいい、コロ軸受用とはコロを介するものをいう。
そして、台枠へのはまり込みや輪心への接触方法は同様であるから、両者の相違は受金とコロとの相違であって、他はほとんど同様である。
第88図は平滑軸受箱を、また第89図はコロ軸受箱を示す。
コロ軸受の利点は
@ 出発抵抗の減少
A 走行抵抗の減少
B 潤滑剤の節約
C 保守費努力の節減
D 発熱故障の防止
にあるものとされるが、戦後本格製作に着手し大量生産に移ったばかりの製作技術では、適確なるグリースの欠乏と相まって、発熱故障の防止に幾分の難点あり、引いては保守努力費の節減にも充分な効果をあげ得なかったが、最近においては製作技術の向上とともに漸次上記各利点をあげつつある。 |
第88図 平滑軸受箱 第89図 コロ軸受箱
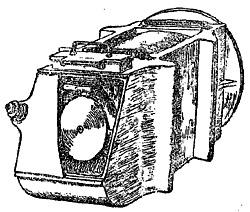 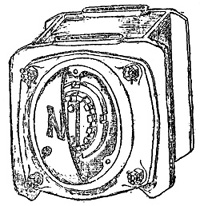 |
以上のうち、出発抵抗及び走行抵抗の減少は球軸受またはコロ軸受の最大の特徴ともいうべきものであって、その原理はおよそ次の通りである。
球軸受またはコロ軸受は滑り摩擦を転がり摩擦に入れ換えるために考案されたものであって、その推進力(注6)は加えられる圧力と、転がり摩擦に比例し、円筒の半径に反比例する。
(注6)
半径rの円筒を平面上に横たえ、圧力pを加えつつ滑ることなく転がす場合の抵抗モーメントをMとすれば
M=f・pであるが、もしこれに垂直に且つ平面に平行して推進力Tを与えるものとするとT=f・p/rである。
この場合 f を転がり摩擦係数という。
転がり摩擦係数は滑り摩擦係数(0.01〜0.15)よりも非常に小さく、球軸受は0.002〜0.003、コロ軸受は0.005〜0.008であって前者は約1/50後者は約1/20である。
球軸受は点接触であるが、コロ軸受は線接触で圧力を受ける面積が大きい。
従ってコロ軸受は同一寸法の球軸受に比べて負荷重・衝撃及び一時的過負荷に耐える性質をもっている。
また、球軸受は起動の摩擦係数と運動の摩擦係数とに差異がないが、コロ軸受は両端に推力(注7)がかかる関係上速度が大となると摩擦係数は小さくなる。
(注7) 軸方向に押す力を推力という。
以上のような理由で、車軸にはコロ軸受を、補助回転機軸には球軸受が用いられるのである。
第90図は動輪用コロ軸受を、また第91図は先輪軸用コロ軸受のそれぞれ構造を示す。
前者は140mm円錐コロ軸といい、後者は120mm円錐コロ軸という。
最初の寸法はそれぞれ、車軸の直径を称するもので、コロはともに1列17本を並べた円錐復列形を用いる。
ただ動輪軸に対してはコロ内輪が車軸と平行したものを用いるが、先輪軸用には内輪は円錐形をなし、更にその内側にスリープを挿入して、これをナット(左端)で締めつけ、キーをはめて固定する。
大体コロ軸受にはスリーブ付のものとスリーブ無しものとの2種類がある。
車軸の仕上げ精度の低いものに対してはスリーブを用いてこれを補正するのに使うのを常とするが、精度が高い即ち車輪旋盤もしくは研摩設備を完備することができる場合はスリーブ無しを用いる方が仕上りが確実である。
電気機関車の場合は、スリ−ブ付で出発した電車・客車などとの互換性をもたせるために先輪軸に対してはこの方法を用いるが、動輪軸にては上記の理由でスリープ無しが用いられるようになったのである。
コロ軸受は保守に手数を要しない特徴を有するというが、これには高度の組立かたを要することと、適切な潤滑油の選定と給油方法が伴なわなければならない。
組立技術即ち装填順序と方法については省略するが、給油について少し説明を加えよう。
球軸受の完全なものは潤滑剤を使用しない場合に却って摩擦係数が小であり、潤滑剤の粘度が大きくなるに従い摩擦係数は増加する。
しかし、潤滑剤を用いないと球に錆を生じて球面の円滑を傷け、摩擦係数が著しく増大するので潤滑剤が使用されるのである。 |
第90図 動輪用コロ軸受
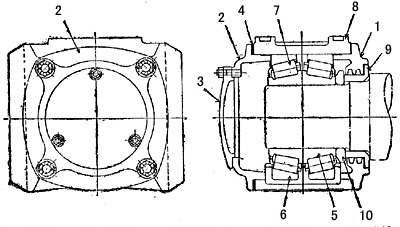
1 内蓋、2 前蓋、3 検査蓋、4 シム、5 内輪
6 外輪、7 コロ、8 体、9 塵除座、10 鍔
第91図 先輪軸用コロ軸受
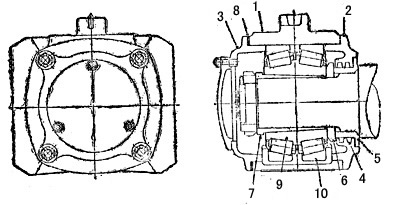
1 体、2 内蓋、3 前蓋、4 塵除、5 塵除座
6 パッキン、7 スリ−ブ、8 挾金、9 内輪、10 外輪 |
しかし、コロ軸受についてはコロの両端に推圧を受けるので潤滑剤を用いる必要がある。
グリースは軽質の純鉱物性油が適当であって、現在車軸用としては極圧グリースが指定されている。
グリースを過量につめこむことはコロの転動を阻止するから適量を用いるように注意せねばならない。
top
***************************************
|